UNIVERSIDADE FEDERAL DO PARÁ INSTITUTO DE TECNOLOGIA PROGRAMA DE PÓS-GRADUAÇÃO EM ENGENHARIA ELÉTRICA
Texto
Imagem
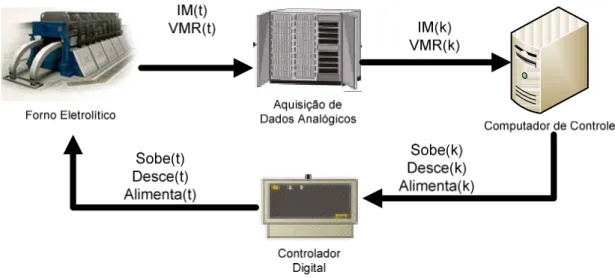



Documentos relacionados
Se lançar o dado duas vezes e adicionar os números saídos, qual é a menor soma que
aditivos exceto aditivos de prorrogação de prazo contratual com qualquer terceiro, com vaDeliberações: As acionistas da Companhia, por unanimidade de votos, após debates e dis-
O Conselho Federal de Psicologia (CFP) apresenta à categoria e à sociedade em geral o documento de Referências Técnicas para a Prática de Psicólogas(os) em Programas de atenção
Dessa forma, diante das questões apontadas no segundo capítulo, com os entraves enfrentados pela Gerência de Pós-compra da UFJF, como a falta de aplicação de
Para Azevedo (2013), o planejamento dos gastos das entidades públicas é de suma importância para que se obtenha a implantação das políticas públicas, mas apenas
Janaína Oliveira, que esteve presente em Ouagadougou nas últimas três edições do FESPACO (2011, 2013, 2015) e participou de todos os fóruns de debate promovidos
Foram analisados a relação peso-comprimento e o fator de condição de Brycon opalinus, em três rios do Parque Estadual da Serra do Mar-Núcleo Santa Virgínia, Estado de São
Ninguém quer essa vida assim não Zambi.. Eu não quero as crianças