Aplicação da metodologia FMEA para revisão de estratégias de manutenção em equipamentos de perfuração de uma mineradora [manuscrito] / Mateus Batista Zanetti. APLICAÇÃO DO MÉTODO FMEA PARA REVISÃO DAS ESTRATÉGIAS DE MANUTENÇÃO DE EQUIPAMENTOS DE PERFURAÇÃO EM EMPRESA DE MINERAÇÃO Membros do Painel. Este estudo propõe a aplicação do método "FMEA - Failure Mode and Effects Analysis" - Análise do Modo de Falha e Efeitos - em um sistema específico do equipamento de perfuração de uma mineradora para revisar as estratégias de manutenção e reduzir o número de falhas.
Com base nisso, as estratégias de manutenção existentes foram revistas com o objetivo de alcançar os melhores resultados em termos econômicos e operacionais. Compreendendo os principais modos de falha desses ativos, bem como suas causas e efeitos, é possível propor uma revisão das estratégias de manutenção para auxiliar na tomada de decisões mais seguras.
Objetivos
Objetivo Geral
Outro ponto importante diz respeito ao comprometimento da equipe de manutenção em relação às diretrizes estratégicas definidas. Mesmo que haja uma gestão que determine como deve ser realizado o processo de manutenção de ativos, muitas vezes isso não é feito pelos executores de forma completa e sistemática, ou por falta de instruções, controles ou conhecimentos específicos adequados para a realização das atividades. . Defeitos decorrentes da montagem do componente ou do processo de fabricação geralmente interferem na vida útil e no desempenho do equipamento.
Objetivos Específicos
O presente trabalho pretende utilizar as metodologias propostas pela Manutenção Centrada em Confiabilidade (MCC) para aumentar a confiabilidade de equipamentos de perfuração importantes no processo de extração de minério de ferro de uma grande mineradora. Para a saúde do equipamento, é antes de tudo importante que o pessoal de manutenção aja sistematicamente em caso de mau funcionamento, ou seja, concentre suas intervenções nas causas dos problemas e menos nas consequências e prolongue sua vida útil. Para isso, além de controles e planejamentos bem definidos, é de extrema importância o entendimento de estratégias estruturadas de tomada de decisão, por exemplo, para determinar o melhor momento para implantação de medidas corretivas, preventivas, preditivas e a periodicidade das inspeções.
Justificativa
Organização do trabalho
Determinar os modos e efeitos de falhas, funções, níveis de severidade dos componentes aplicando a metodologia FMEA; O capítulo 5 traz os resultados e discussões obtidos durante a aplicação da metodologia, e por fim as conclusões no capítulo 6.
Gestão da Qualidade
Confiabilidade
A confiabilidade, por sua vez, um dos conceitos fundamentais observados nas dimensões da qualidade, é definida por Scapin (1999) como a probabilidade de que um sistema ou produto desempenhe sua função satisfatoriamente a partir de um determinado intervalo de tempo e sob circunstâncias específicas de trabalho.
Manutenção Centrada na Confiabilidade
FMEA
Além disso, segundo Firmino et al. 2004), a confiabilidade é uma ferramenta que permite a elaboração de estratégias de manutenção, pois visa garantir o bom funcionamento do produto, em detrimento do tempo de operação e dos fatores que podem influenciar no seu funcionamento. desempenho. O uso consistente da FMEA pode possibilitar a identificação de problemas não previstos e, conseqüentemente, estabelecer prioridades para correção (Palady (1997)). Função: O que o usuário deseja que o item ou sistema faça dentro de um padrão de desempenho especificado.
Por fim, conforme definido por Xenos (1998), o objetivo final desta ferramenta é criar um plano integrado de manutenção que aumente a qualidade e a produtividade das empresas. As estratégias de manutenção são definidas a partir de uma lógica de decisão estruturada pelo MCC, na qual são priorizadas ações que demonstrem maiores ganhos em confiabilidade, redução de custos, redução de riscos à saúde e segurança e eficiência operacional. Inspeção Preditiva (PI): Uma inspeção planejada de um item para procurar sinais específicos de falha potencial.
Inspeção Funcional (FI): Tarefa realizada em intervalos específicos para identificar a ocorrência de uma falha funcional que não é aparente para a equipe operacional em suas atividades normais. Reparo Preventivo (RP): Restauração da condição de um item antes de um determinado limite de idade. Substituição Preventiva (SP): Retirar um item de serviço e substituí-lo antes de um determinado limite de idade.
Reparo Funcional (RF): Decisão de usar o item até que ele falhe e depois repará-lo ou substituí-lo.
Trabalhos Correlatos
Por fim, Herpich e Fogliatto (2013) desenvolveram a metodologia FMECA em equipamentos críticos de um sistema de controle e instrumentação de turbogerador. A tabela de métodos foi elaborada com foco na classificação dos modos de falha mais críticos com base nos critérios de segurança, meio ambiente, perdas de produção e custos de manutenção. Como resultado, foi possível definir as melhores estratégias de manutenção possíveis, otimizar planos de manutenção, reduzir custos com manutenções corretivas e preventivas e aumentar a confiabilidade dos equipamentos.
Método
Definição do sistema a ser priorizado e início do preenchimento da tabela FMEA 11
A partir do histórico de falhas da organização, identifique o sistema e conjunto com o maior número de falhas a priorizar para investigação e a lista de seus conjuntos e elementos/componentes. A análise foi realizada com base no número de falhas na frota de perfuração e não no tempo de manutenção, pois o indicador de confiabilidade identificado com valores insatisfatórios, Tempo Médio Entre Falhas (MTBF), é calculado com base no número de intervenções corretivas no equipamento. Foi feito a partir do banco de dados do histórico de falhas da frota e de reuniões entre os responsáveis pelas diferentes áreas de manutenção.
Efeito catastrófico: aquele que pode causar morte humana, perda do sistema principal devido a, por exemplo, explosões ou incêndios ou grandes danos ao meio ambiente. Efeito crítico: ferimentos graves em pessoas ou danos significativos ao sistema ou ao meio ambiente. Efeito marginal: Menos danos às pessoas ou menos danos ao sistema ou ao meio ambiente.
Efeito mínimo: consequências operacionais, ambientais e de segurança abaixo dos níveis máximos exigidos por normas ou leis. Efeito insignificante: falha insuficiente para causar danos às pessoas, sistema, ambiente e contexto operacional. Na sequência, é indicado o grau de detecção do modo de falha relevante, conforme mostra a Figura 4.
Por fim, o RPN é calculado multiplicando os valores detectados por gravidade, frequência e detectabilidade, permitindo que os defeitos com maior RPN sejam priorizados, conforme Tabela 1.

Revisão e criação das estratégias de manutenção
É óbvio que a estratégia que funciona para prevenir a ocorrência da condição de falha sempre será a desejada, pois dessa forma se obtêm maiores ganhos de confiabilidade. A lógica de decisão utilizada pelo MCC sugere uma ordem de preferência entre as atividades que serão aplicadas à condição de falha em análise, priorizando a maximização dos resultados operacionais, financeiros e de saúde e segurança. A mineração é um processo fundamental no mundo moderno, pois o minério de ferro é utilizado como principal matéria-prima para a fabricação de itens indispensáveis à sociedade.
No Brasil, especificamente, a atividade exerce grande impacto econômico no país, pois representa grande parte do PIB brasileiro. A empresa estudada tem sede no Brasil e está presente em outros 37 países, sendo uma das maiores produtoras de minério de ferro do mundo. A mina considerada como objeto deste estudo está presente no estado de Minas Gerais e é responsável por uma parte importante da produção de minério da região.
Nesta fábrica, os processos de aquisição, processamento e produção de materiais são realizados via transporte ferroviário para as principais zonas portuárias do país. Resumidamente, o processo de extração do minério é feito inicialmente com a quebra do solo, a abertura de furos e o uso de explosivos. Com o material mais fragmentado, escavadeiras e pás carregadeiras transportam o material para caminhões, que por sua vez o transportam até o britador, com destino ao processamento na fábrica.
Nesse contexto, os equipamentos de perfuração têm papel fundamental no processo de extração mineral, pois fazem furos no solo para detonação com material explosivo.
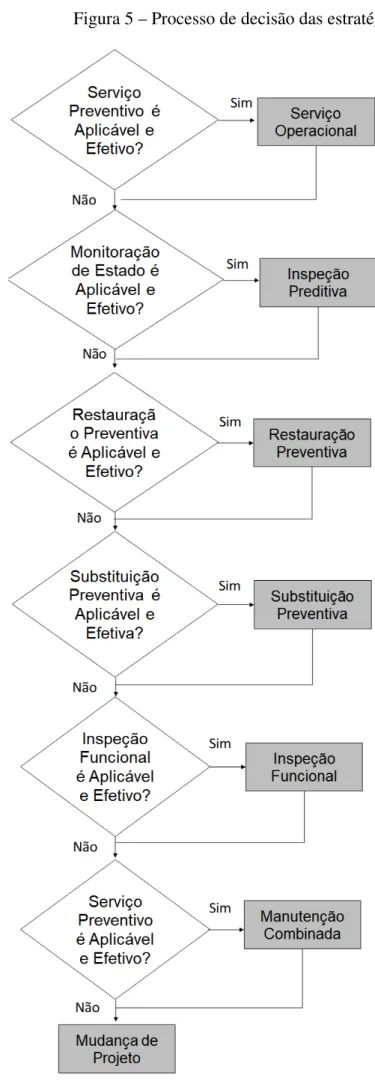
Definição do sistema
Isso mostra que, embora o sistema elétrico tenha apresentado mais falhas no período analisado (46 intervenções corretivas), ele não foi selecionado para a obra por dois motivos. Primeiro, o sistema elétrico em equipamentos de perfuração é muito complexo, pois inclui um número muito grande de subsistemas e componentes e participa de várias funções do equipamento. Outra coisa é que o trabalho nesse sentido demandaria muito tempo de estudo e desenvolvimento, e por decisão da direção da organização, a implantação da metodologia deveria ser em menor tempo, devido à importância do tema para o contexto operacional.
Com base nas condições apresentadas, o sistema de bloqueio de mastro, que apresentou o segundo maior número de erros (32 intervenções corretivas), foi escolhido para o estudo. Em resumo, o sistema de bloqueio do mastro inclui vários componentes que geralmente contribuem para a função principal do. Sabe-se que o não travamento do mastro implica, entre outras coisas, na impossibilidade de processar a haste para perfurar o terreno.
Fortalecer o entendimento desse sistema entre os colaboradores foi fundamental para as demais etapas do desenvolvimento do método.
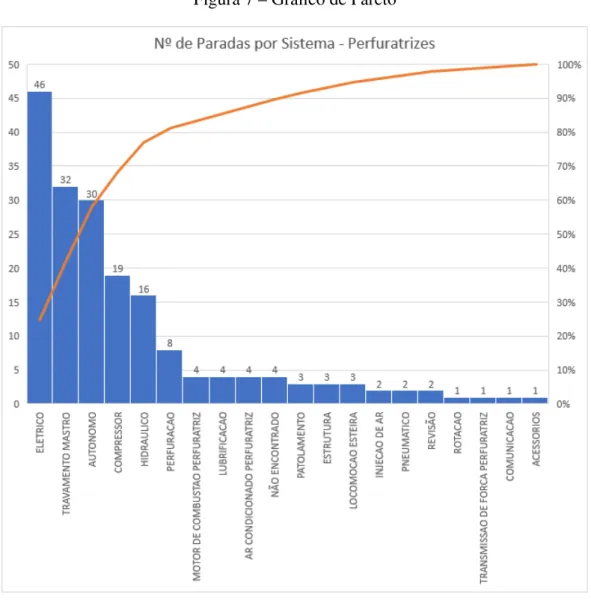
Diagrama organizacional do sistema
Definição das funções, falhas funcionais, modos de falha, efeitos e cau-
Para determinar o grau de risco, os critérios explicados anteriormente foram avaliados com base nas informações coletadas da equipe de manutenção e consultando o histórico de falhas e reparos nos últimos 2 anos. Parte da tabela FMEA desenvolvida no trabalho está ilustrada na Figura 9 e Figura 10. Figura 9 – Tabela FMEA.
Revisão e criação das estratégias de manutenção
Orientamos os responsáveis a alterar os planos de manutenção no sistema SAP, de acordo com as atividades propostas. Os planos de manutenção funcionam como um manual para toda a equipe envolvida nas atividades, tanto na execução quanto na programação e gestão. Isso é importante para garantir e orientar as equipes de manutenção a seguir e aderir ao que está especificado nos planos.
Percebe-se que esse comportamento repetitivo de falhas ocorre na maioria das vezes devido às condições extremas de operação desse equipamento (exposição a sujeira, iluminação irregular, alto esforço mecânico, entre outros) ou por não possuir estratégias adequadas de prevenção ou controle de manutenção. Espera-se que as ações de manutenção propostas a curto ou longo prazo afetem a redução gradual dos riscos, principalmente os mais importantes. A reparação preventiva era 21 e passou para 35, e a substituição preventiva, que era 23, evoluiu para 30, reforçando o perfil mais preventivo das atividades de manutenção propostas.
Portanto, com a aplicação do FMEA, foi possível otimizar os planos de manutenção e aumentar a eficiência da manutenção do sistema de bloqueio de massa. A aplicação do FMEA no sistema de travamento em massa dos equipamentos de perfuração de uma mineradora mostrou que é possível aumentar a confiabilidade deste equipamento, a partir da implementação de estratégias de manutenção adequadas que gerem resultados em custo e desempenho. Relacionado a isso, a ferramenta auxilia na otimização da rotina de manutenção e na preservação da saúde dos ativos, pois contribui para uma atuação cada vez mais preventiva nos equipamentos e no comprometimento e envolvimento direto da equipe de manutenção.
A implementação de planos de manutenção mais estruturados e confiáveis minimiza gastos excessivos com intervenções corretivas ou perdas irreparáveis de componentes. Além disso, as atividades de manutenção propostas podem mudar de acordo com os objetivos estratégicos da organização ou o desenvolvimento de novas tecnologias para o setor de manutenção de equipamentos de mineração. Aplicação do fmeca para definir estratégias de manutenção em um sistema de controle e instrumentação de turbogerador. Revista Iberoamericana de Engenharia Industrial, v.
