ANÁLISE COMPARATIVA DA QUALIDADE NA PERFURAÇÃO DE ALUMÍNIO 7075-T6 COM AÇO RÁPIDO E BROCAS HELICOIDAIS DE CARBONETO. Portanto, este trabalho tem como objetivo analisar a qualidade do furo produzido por uma broca de aço rápido e uma broca de metal duro em alumínio 7075-T6.
Objetivos
Objetivo Geral
Objetivo Específico
Processo de Furação
Brocas Helicoidais
Para Stemmer (2005), a seleção da categoria adequada neste processo deve levar em consideração os seguintes fatores: diâmetro do furo, profundidade, formato e tolerâncias de medição e volumes de produção. permitir que o fluido de corte alcance as bordas. Esses canais são usinados ou moldados no corpo da broca para formar as arestas de corte. f) Arestas de corte: em uma broca helicoidal, as duas arestas de corte principais não se encontram em um ponto, mas há uma terceira aresta conectando-as.
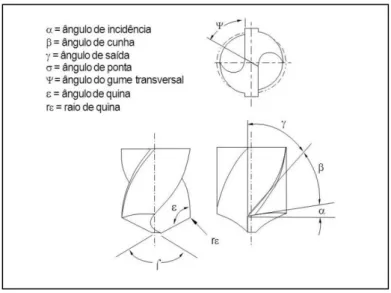
Materiais das brocas inteiriças
Brocas de aço rápido HSS – High Speed Steel
A ferramenta de aço rápido pode então ser tratada termicamente para atingir dureza na aresta de corte (65 Rockwell C), enquanto a ferramenta tem boa tenacidade no núcleo. Ferramentas de aço rápido apresentam maior tenacidade do que todos os materiais não ferrosos utilizados na usinagem, principalmente materiais de metal duro e cerâmicos (GROOVER, 2014).
Brocas de WC – Metal duro
As ferramentas HSS são amplamente utilizadas entre os operadores devido ao seu baixo custo e facilidade de reafiação. Ao longo dos anos, foram descobertas melhorias de nitidez para manter as ferramentas competitivas em muitas operações. Além disso, também podem ser revestidos para aumentar significativamente a eficiência de corte (GROOVER, 2014).
A vantagem do metal duro sobre o aço rápido é que ele tem vida útil mais longa (mais de 10 vezes), permite maior velocidade de corte (cerca de 2,5 vezes) e velocidade de avanço (cerca de 2 vezes) (WICK, 1983). As brocas de metal duro também podem ser revestidas para prolongar sua vida útil e obter propriedades mecânicas superiores (MACHADO, ABRÃO, COELHO, SILVA, 2011).
Afiações para brocas helicoidais
Brocas de metal duro também podem ser revestidas para prolongar sua vida útil e obter propriedades mecânicas superiores (MACHADO, ABRÃO, COELHO, SILVA, 2011). que aumenta após reafiações sucessivas. Seu objetivo é reduzir o superaquecimento na parte externa das arestas de corte, onde a velocidade de corte é maior. Esta afiação provou dar bons resultados na perfuração de ferro fundido cinzento. Perfurada, deve ser utilizada em furos rasos (menos que o dobro do diâmetro da broca). Ângulos grandes causam mais desgaste na circunferência e um ângulo secundário de 90° pode ser usado.
Este tipo de retificação visa reduzir rebarbas na saída do furo, melhor posicionamento do centro do furo e reduzir tempos de usinagem por ter menor comprimento de ponta.
Qualidade no Processo de Furação
- Rebarbas
- Tolerâncias Geométricas
- Tolerâncias de Forma
- Rugosidade
Na maioria dos casos, as rebarbas são definidas como saliências indesejadas de material formadas como resultado do fluxo plástico das operações de corte (AURICH et al., 2009). No processo de furação, rebarbas são geradas na superfície superior e na superfície inferior da peça (furo passante). Para Silva Neto (2018), as tolerâncias de forma são desvios que um elemento pode apresentar em relação à sua forma geométrica ideal.
A tolerância de cilindricidade inclui as tolerâncias permitidas na seção longitudinal do cilindro, que inclui conicidade, concavidade e convexidade. Em geral, pode ser definido como o desvio de um determinado elemento (ponto, linha, plano) em relação à sua posição teórica. Tolerância de posição de um ponto: delimitado por um círculo de diâmetro “t”, com centro na posição teórica.

Usinabilidade dos Materiais
- Usinabilidade nas Ligas de Alumínio
- Liga de Alumínio 7075
- Quanto a Seleção das Ferramentas para Alumínio
- Quanto aos Parâmetros de Usinagem no Alumínio
Para um bom tratamento superficial, deve-se atentar para a velocidade de corte e verificar também a geometria da ferramenta. Para Santos e Sales (2007), a usinabilidade do alumínio puro representa uma alta ductilidade que leva à produção de um cavaco contínuo e em grandes áreas de contato do cavaco com a ferramenta, resultando em uma elevada força de corte. Alta resistência e fácil afiação proporcionam arestas de corte afiadas, mantendo as forças de usinagem em níveis baixos. b) Metal Duro: A classe K é preferida, o material base desta classe é o carboneto de tungstênio.
Velocidade de corte: A velocidade de corte deve ser a mais alta possível para reduzir custos, tempo de processamento, reduzir a formação de aresta de corte postiça, os cavacos também quebram melhor e o acabamento superficial melhora. Profundidade de corte: Deve ser a maior que a ferramenta e os limites da ferramenta permitirem, normalmente usando profundidades maiores que 0,6mm para desbaste e menores que 0,6mm para operações de acabamento. Este trabalho realizou uma série de experimentos que buscaram avaliar a qualidade do furo criado no processo de furação da liga de alumínio 7075 – T6, variando os parâmetros de velocidade de corte, avanço e dois materiais comumente utilizados em ferramentas de corte.
Materiais
Ferramentas
Equipamentos
A máquina também foi utilizada para medir as bordas formadas na saída dos furos. Para medir a qualidade dos furos produzidos foi utilizada uma máquina de medição tridimensional fabricada pela ZEISS, modelo ACCURA, que possui o software CALYPSO. Para medir a rugosidade, as amostras de teste tiveram que ser cortadas ao meio.
Para determinar o ponto zero da peça durante a usinagem foi utilizado um apalpador RENISHAW modelo RMP-60 com diâmetro de esfera de 6 mm.
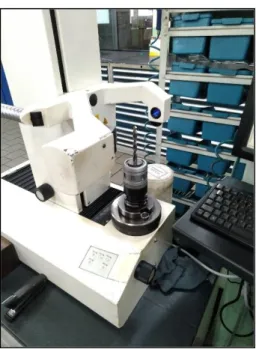
Corpo de prova
Parâmetros de corte e ensaios realizados
A Tabela 4 mostra os parâmetros utilizados para perfurar o corpo de prova com a broca de aço rápido (HSS). A furação foi realizada diretamente, sem retornos para retirada de cavacos e resfriamento da ponta da broca (pica-pau).
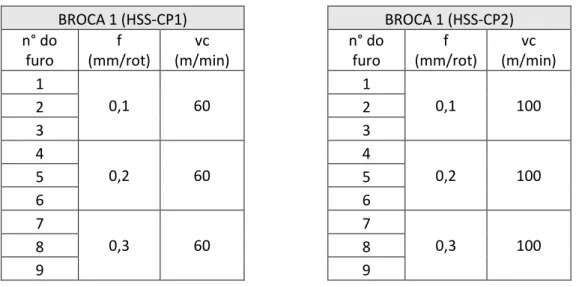
Métodos
- Fixação e verificação do alinhamento do corpo de prova
- Medição e preparação das brocas
- Medição dos erros de posição dos furos
- Medição das rebarbas
Antes de preparar as brocas nos cones de montagem foi medido o diâmetro das brocas, foram feitas medições na ponta e haste, para medir foi utilizado um micrômetro com resolução de 0,01 mm, e também foi medido o ângulo da ponta das brocas. . usando um goniômetro. As brocas foram fixadas por meio de cones hidráulicos autoengatantes, mantendo todo o sistema de ferramentais rígido. O desvio da ferramenta foi verificado na máquina DMG VIO 210 (Microset), o desvio não deve ultrapassar 20 mícrons ou 0,02 mm (SANDVIK, 2022).
Foram realizados três testes para cada condição testada, conforme parâmetros previamente apresentados nas tabelas 4 e 5, conforme mostra a figura 22. Conforme figura, para cada velocidade de corte (Vc1) foram utilizados três avanços (f1-0,1mm/rot., f2- 0,2mm/rot. e f3-0,3mm/rot.), três furos foram usinados para cada condição testada. A medição da rebarba foi feita apenas na saída do furo, utilizando o projetor óptico de perfis, máquina DMG VIO 210 (Microset), gerando uma média da altura da rebarba para os três ensaios para cada condição.
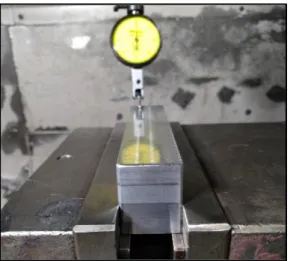
Diâmetro das Furações
Nas Figuras 24 e 25 é possível observar que a broca de metal duro em ambas as condições apresentou diâmetro de furo maior para a maioria das condições testadas. A broca de aço rápido, na condição de maior velocidade de corte, conforme Figura 25, apresentou maior variação de medida em relação ao diâmetro médio em comparação à broca de metal duro. A Figura 26 mostra uma comparação da broca de aço rápido operando em velocidades de corte baixas e altas.
Por outro lado, é possível observar uma redução no diâmetro com o aumento do avanço para maiores velocidades de corte (100m/min). A Figura 27 mostra uma comparação da broca de metal duro operando em velocidades de corte baixas e altas. Para a broca MD, o aumento do avanço não teve influência significativa no diâmetro do furo.
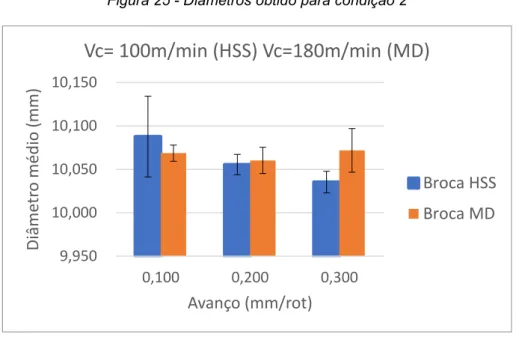
Circularidade das furações
Para brocas de metal duro, é possível observar um pequeno aumento na circunferência com o aumento do avanço. Na Figura 29 é possível observar que, para a condição 2, apenas para o avanço de 0,1 mm/rotação, a broca HSS apresentou resultado de circularidade superior em relação à broca de metal duro. É também evidente que à medida que a taxa de alimentação aumentou, o exercício HSS mostrou uma redução ou melhoria na circularidade.
Para brocas de metal duro de alta velocidade, o fator de avanço não apresentou grande influência na circularidade. Em geral, para a broca HSS, ambas as velocidades de corte testadas apresentaram melhor circularidade em avanço igual ou superior a 0,2 mm/rotação. Com a broca MD, o avanço aumentou a circularidade em quase todos os resultados e a velocidade de corte não pareceu ter grande importância.
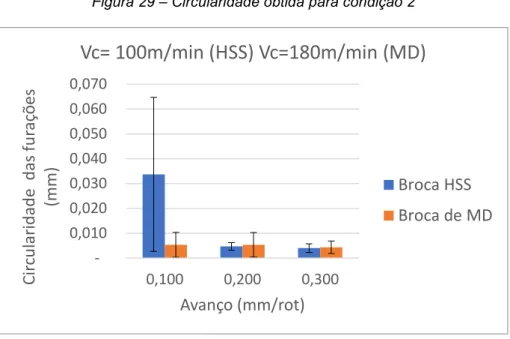
Desvio ou Posicionamento das furações
Na Figura 30, para a condição 1, a broca de metal duro aumentou gradativamente seu desvio com o aumento do avanço, em contrapartida, a broca HSS apresentou o melhor resultado com o maior avanço. Nesta condição, observa-se que, para a broca HSS, o posicionamento melhorou gradativamente à medida que o avanço aumentou, enquanto para a broca de metal duro, apenas para f=0,2 mm/rot, apresentou melhor resultado. No geral, para a broca HSS, à medida que o avanço aumentou, houve uma redução na deflexão da broca para a maioria dos resultados e, à medida que a velocidade de corte aumentou, também reduziu a maioria das deflexões da broca.
Para a broca MD, o aumento do avanço causou aumento no desvio para baixa velocidade de corte, enquanto o avanço em alta velocidade de corte apresentou melhora nos desvios, o efeito da velocidade de corte, quando aumentada, os valores de desvio reduzem para a maioria dos resultados. O melhor posicionamento de 0,027mm foi encontrado pela broca HSS com vc=60m/min ef=0,3mm/rot. Para brocas de metal duro, o melhor posicionamento encontrado foi 0,031mm com vc=180m/min ef=0,2mm/rot.

Rugosidade das furações
Em geral, ao aumentar o avanço da broca HSS, notou-se um pequeno aumento na rugosidade; o aumento da velocidade de corte só foi significativo para o avanço de f=0,2 mm/rot, para os demais avanços não foi significativo. provou ser significativo. Na broca MD, a rugosidade aumentou gradativamente à medida que a velocidade de corte progrediu em baixa velocidade de corte, enquanto apresentou melhora em alta velocidade. A velocidade de corte teve um impacto significativo na melhoria da rugosidade, especialmente para avanços de f=0,2 - 0,3 mm/rot.
O melhor resultado em termos de rugosidade foi obtido para a broca de metal duro com vc=180m/min e f=0,2 e 0,3mm/rot.
Rebarbas na saída das furações
Em geral, para a broca HSS, o aumento do avanço entre 0,1 e 0,2 mm/rotação resultou em uma tendência de aumento das arestas na saída do furo, enquanto o aumento da velocidade de corte não pareceu ser significativo. Para a broca MD, a mudança de avanço não apresentou resultados significativos, mas apresentou o pior resultado com f=0,2 mm/rot para vc=180 m/min. A broca HSS apresentou menor geração de rebarba para vc=60 m/min e f=0,1 mm/rot, onde produziu rebarba de 0,16 mm.
Com o aumento da velocidade de corte, notou-se redução nos diâmetros para todos os avanços na broca MD. Para posicionamento, ambas as brocas ofereceram valores semelhantes, mas a broca HSS ofereceu a melhor posição do furo. A broca MD apresentou a menor formação de rebarbas para todos os testes realizados e com os menores valores de desvio padrão.
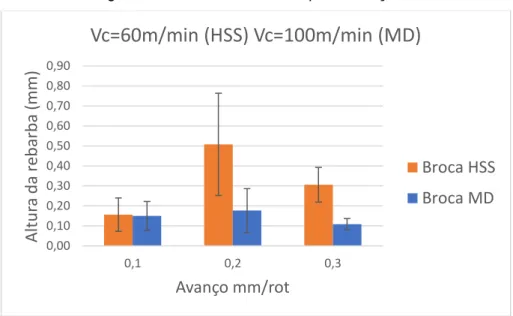