The single NiTi wire samples with a long embedded length were subjected to the pull-out test to study the effect of martensitic transformation/reorientation on the dissolution initiation and also on the dissolution propagation. From in-situ observations, the decomposition starts from the wire entry point and continues to the embedded end. The dissolution rate was found to depend on the displacement rate as well as the length change during phase transformation.
It has been established that the martensitic transformation occurring in the wire affects the mechanical behavior of the composite specimens. In this way, using wire with higher transformation stress increases the composite tensile strength. In this paper, samples with complex geometry were designed and fabricated in order to evaluate the elastic properties of the composite material in two directions (perpendicular and parallel to the axis of the wire).
The heterogeneous displacement/strain fields created due to the complex geometry of the composite samples were measured. Furthermore, the numerical strain fields obtained using the identification parameters were compared with the experimental ones.
- General Properties
- Introduction
- Martensitic phase transformation
- Shape memory effect (SME)
- Superelasticity (SE)
- Martensitic transformation in NiTi based alloys
- State of the art of SMA composites
- SMA-Polymer composite
- SMA/metal matrix composites
- Identification techniques and Digital Image Correlation
- Techniques d‟identification
- Techniques de mesure de champs cinématiques
- Objectives
- Materials description
- SMA wire
- Epoxy matrix
- Sample preparation
- Pull-out test
- Uniaxial tensile test
- Heterogeneous test
The mold is used to prepare the simple tensile samples and the samples with complex geometry.
Characterization of the matrix/wire interface- influence of the
- Analytical method
- Effect of martensitic transformation on debonding initiation
- Effect of martensitic transformation on debonding propagation
- Conclusion
3.9-b and 3.12-c, the power is divided by transformation load and the DR is divided by the average rate.
Tensile properties: characterization and micromechanical
Model development
Numerical results
Discussion
- Comparison of micromechanical and experimental results
- Effect of martensitic transformation on the mechanical behavior
- Effect of martensitic transformation on the debonding mechanism
Conclusion
This model helps to understand the influence of martensitic transformation on the global behavior of composite samples at different temperatures. It shows that the behavior of composite materials made with three different wires is strongly influenced by the properties of the wire (Figs. 4.1 and 4.2). Therefore, the mechanical behavior of the composite will be a compromise between these two factors, depending on the test temperature and the volume fraction of the wire.
As expected, the tensile strength of the composite increases with increasing wire volume fraction. In addition, the model did not take into account the reduction of the wire diameter due to the martensitic transformation. As mentioned in the previous section, the model used the experimental behavior of the wire and die by introducing a secant modulus.
The effect of martensitic transformation was taken into account in the micromechanical model by introducing the experimental stress-strain of the wire under different conditions. This figure shows that the beginning of the stress plateau (for the wires) corresponds to the beginning of the second part in the behavior of the composite. It could be concluded that the martensitic transformation taking place in the wire affects the overall behavior of the composite.
Since the entire uniform part of the pattern is elongated, the MT must appear at several points in the wire at. The fact is that the martensitic transformation takes place under greater stress in a wire heat-treated at a lower temperature; and due to the higher stress plateau, the overall behavior of the composite sample improved in this case. As expected, increasing the wire volume fraction improves the mechanical behavior of the composite samples.
From the experimental or micromechanical results, two trends are observed in the stress-strain behavior of the composite samples. It was claimed that the martensitic transformation in the wire occurs simultaneously at several points, so it can follow the matrix displacement as long as the interface remains intact. The transformation stress for the wire in the matrix constraint may be different from the case in which the wire is freely transformed.

Introduction
Inverse Method
Application to the NiTi wire composite
- Convergence and stability analysis
- Convergence test
- Stability analysis
One of these algorithms is Levenberg-Marquardt (LMA) [Levenberg 1944, Marquardt 1963] based on Gauss-Newton. This matrix expresses the sensitivity of the measured quantities with respect to the variation of the identification parameters. In this way, two verifications have been obtained to examine the robustness of the method (convergence test) and its stability (stability analysis).
To verify the robustness of the method, a numerical database is constructed and used instead of the experimental database. This procedure was repeated for different sets of reference parameters (table 5.1) to verify the identifiability of the method for samples with different wire volume fraction. Effect of Mesh Size on Identifiable Parameters Applied Displacement=0.6 mm Identified Parameters.
The evolutions of the cost function and parameters versus the iteration number for three different sets of initial estimates are shown in Figure. Variation of a) the cost function and b) the parameters versus the iteration number for a set with 336 elements and applied displacement = 0.6 mm ; convergence of the larger values. Evolution of a) the cost function and b) the parameters versus iteration number for a set of 336 elements and applied displacement = 0.6 mm; convergence of the larger values.
Set of 336 elements, applied displacement=0.6 mm. Fig. 5.7. Variation of a) the cost function and b) the parameters versus iteration number for a set of 336 elements and applied displacement = 0.6 mm; starting from the values close to the solution. The parameters identified using the perturbed voltage fields are in the same order as the reference parameters. The samples of most samples have been analyzed and the voltage fields have been determined.
Meraghni based on the Mori-Tanaka model and formulations were published elsewhere [Meraghni et al. This matrix expresses the sensitivity of the measured quantities (stresses and loads) to the change of the identification parameters. The numerical study demonstrates the robustness of the inverse method and its ability to be applied to the NiTi wire composite samples studied.
The effect of martensitic transformation on the mechanical behavior of the NiTi-epoxy composite was investigated using a standard tensile test. A micromechanical model was developed to investigate the role of the wire in the composite.
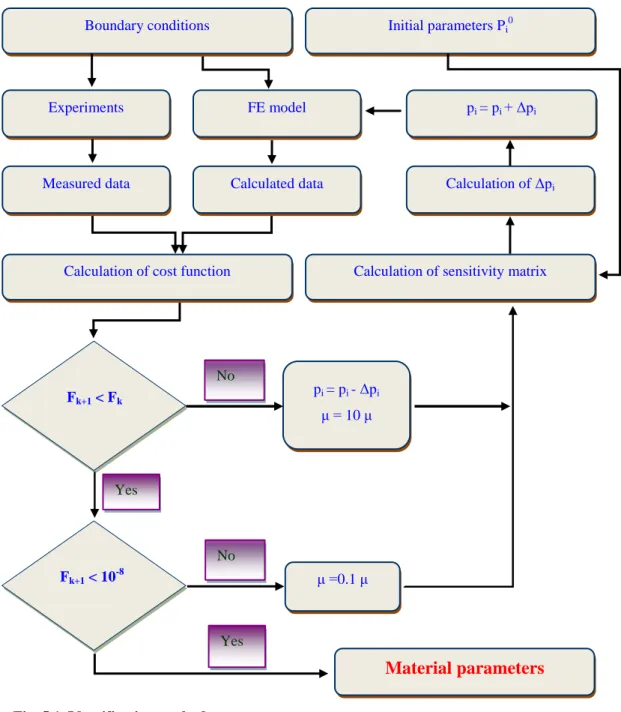
Application for experimental strain fields
Identification results
- Identification results using Correli-Q4
- Identification results using Vic2D
Conclusion
Inverse analysis has been used by Tillier [Tillier 1998] to identify the mechanical behavior of thermoplastic polymers. In the present work, a method is proposed for the identification of the four independent elastic technical constants in the plane E11, E22, G12 and v12 of an orthotropic composite material. In other words, the stability study demonstrates the ability of the method to identify the parameters in the presence of errors.
Actual experimental strain fields are obtained from the heterogeneous testing of the composite samples with different wire volume fractions at room temperature. 157 components were extracted for the coordinates of the elements in the numerical part after correction of the starting point. As expected, it was determined that increasing the wire volume fraction improves the mechanical behavior of the composite samples.
A very regular debonding/unbonding pattern was observed and related to the transformation mechanism of the NiTi wires.
Micromechanical results