Literature Review
Phase Equilibria
- Equilibrium relations
- γ – ϕ Approach
- ϕ – ϕ Approach
- γ – γ Approach
- Azeotropic Binary Mixtures
- Ternary Mixtures
- Residue Curve Maps and Their Classification
- Unidistribution and Univolatility Lines
The activity coefficients, which are functions of temperature and liquid phase composition, can be calculated by different activity coefficient models (Stichlmair and Fair, 1998). In the simple batch distillation of the mixture, the composition of the residue always tends towards the azeotropic composition.
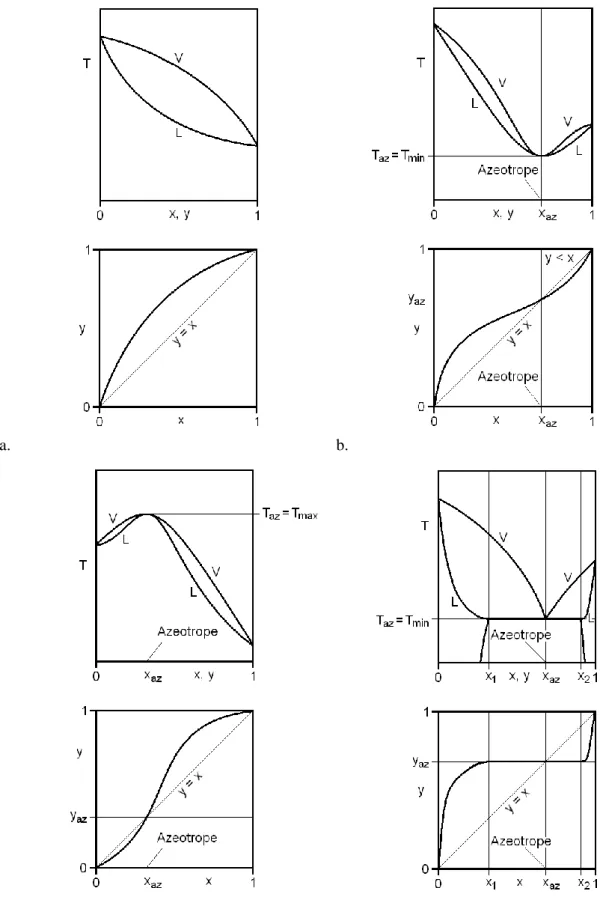
Zeotropic and Homoazeotropic Distillation
- Continuous Homoazeotropic Distillation
- Homogeneous Batch Distillation
- Operational Policies
- Product Sequences for Azeotropic Distillation
- Non-Conventional Configurations
- Off-Cut Recycle
They said that the application of the cyclic operation is advantageous over the traditional one in the case of more difficult separations. The operational parameters of the batch stripper are the reboil ratio (which is analogous to the reflux ratio of batch rectifier, being the ratio of the flow rates of the vapor leaving the reboiler and the product stream) and the liquid flow rate leaving the upper vessel.
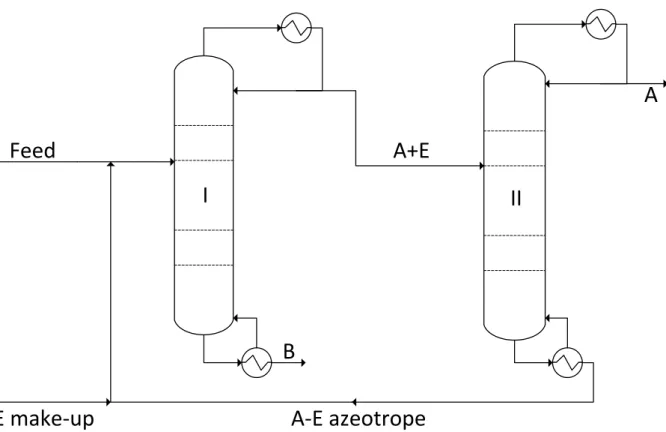
Homoextractive Distillation
- The Role and Selection of the Entrainer
- Continuous Homoextractive Distillation
- Batch Homoextractive Distillation
The effect of the trainer can also be studied using different graphic methods. The upper, the correcting part, separates one of the original components (here A) from the entrainer.
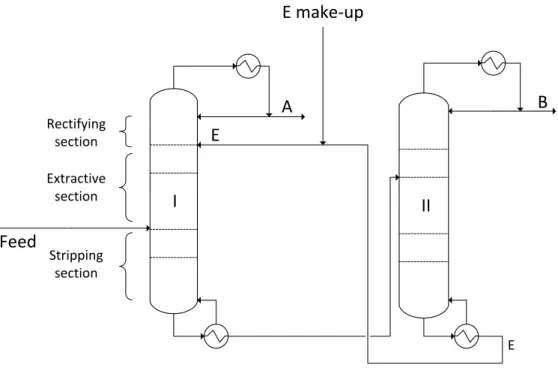
Heteroazeotropic Distillation
- Continuous Heteroazeotropic Distillation
- Batch Heteroazeotropic Distillation
2005a,b) distinguished two strategies for mode II based on the reflux of the entrainer-rich phase. The effectiveness of this tool was also demonstrated on the batch heteroazeotropic distillation separation of the azeotrope toluene – pyridine with water.
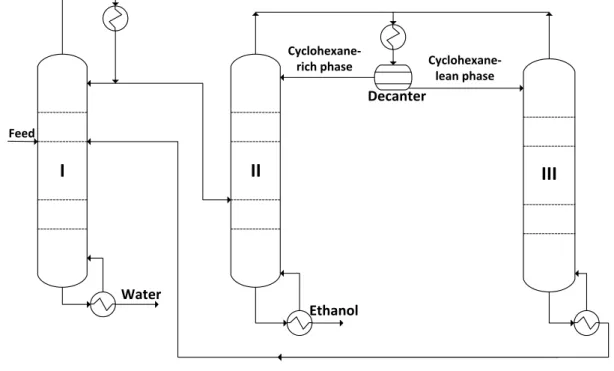
Heterogeneous Extractive Distillation
- Continuous Heterogeneous Extractive Distillation
- Batch Heterogeneous Extractive Distillation
In batch heteroextractive distillation (BHED) or batch heterogeneous extractive distillation, the inductant forms a heteroazeotrope with one of the original components, similar to batch heteroazeotropic distillation, but it is continuously introduced into the column. They described the industrial application of the process for the separation of two unspecified organic compounds using water as the heterogeneous integrator, where the overhead vapor was the binary heteroazeotrope.
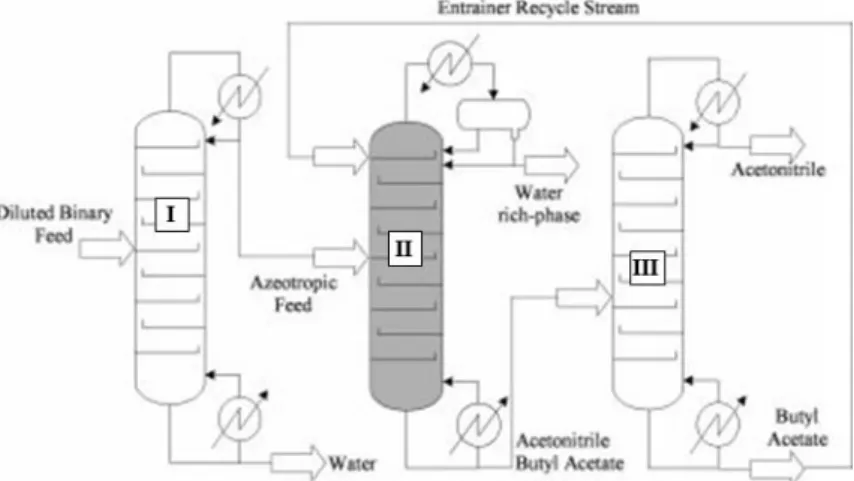
Pressure Swing Distillation
- Continuous Pressure Swing Distillation
- Batch Pressure Swing Distillation
Phimister and Seider (2000b) were the first to study the application of binary PSD in a batch stripper and in a semi-continuous configuration by simulation, for the pressure-sensitive separation of minimum boiling acetonitrile. 2007) were the first to experimentally investigate the application of pressure driven batch distillation (PSBD). Modla and Lang (2010) presented the benefit of thermal integration in the separation of an acetone-methanol mixture in a double column batch stripper.
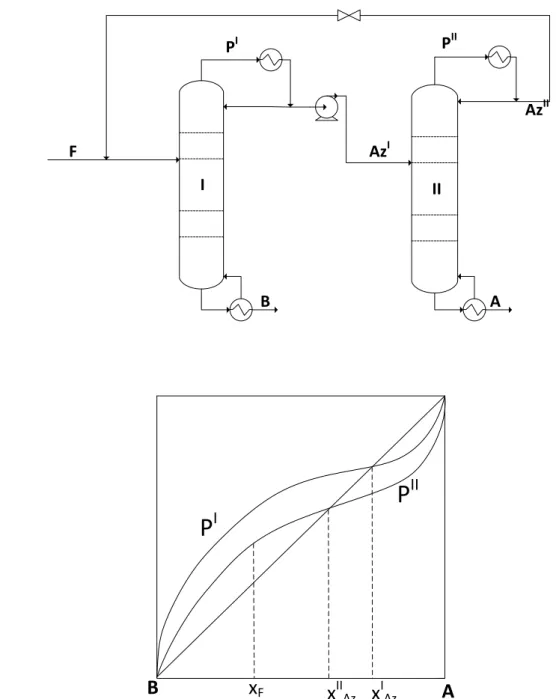
Other Distillation Methods
- Hybrid (Distillation+Absorption) Process
- Salt-Effect Distillation
Development of the level in the upper vessel (closed operating conditions for a batch rectifier N=10, Ropen=9, hold-up: 50 ml/plate).
Algorithm and Program for the Determination of Product Sequences in Azeotropic
Description of the Algorithm
- Step 1: Determination of the Type of All Stationary Points
- Step 1a: Determination of the Type of Stationary Points in Each Ternary
- Step 1b: Unification of Ternary Submixtures to Quaternary Ones
- Step 1c: Unification to Submixtures of Higher Dimension
- Step 2: Completion of Adjacency Matrix
- Step 3: Determination of Product Sequences
- Managing Heteroazeotropes and Pressure Change
The stability of stationary points in quinary submixtures is determined by comparing their stabilities in all (5) quaternary submixtures. An equivalent definition is that the stationary point j is in the unstable boundary group of point i.
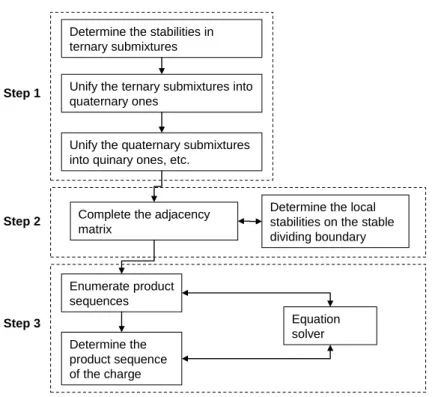
Results
- Calculations for Mixture 1
- Calculations for Mixture 2
A ACMB ACM MB CE C ACE M AC EB E B. The stabilities of fixed points in the different submixtures. The relative amounts of the cuts were determined for two different charge compositions located in different batch distillation regions (Table 2.3). The relative amounts of the cuts were determined for three different charge compositions located in different batch distillation regions (Table 2.5).

Conclusions
The direction of the stationary path for the different operational policies of heteroazeotropic batch distillation. The CHEMCAD model of the batch rectifier with variable liquid holdup in the carafe.
Closed Batch Distillation
Configurations and Operation Modes Studied
- Batch Rectifier (Two-Vessel Column)
- Open Operation Mode
- Closed Operation Modes
- Middle-Vessel (Three-Vessel) Column
- Comparison of the Open Mode of Batch Rectifier and of Middle-Vessel
- Comparison of the Operation Modes of The Middle-Vessel Column
- Multivessel (Four-Vessel) Column
The recoveries of open and different closed modes of the center barrel column are compared under constant energy consumption. The different modes of the mid-vessel column (MVC) without vapor bypass are investigated for the separation of an equimolar mixture (20 dm3) of A, B and C. The open mode of operation of the mid-vessel column is also compared with the different closed ones.
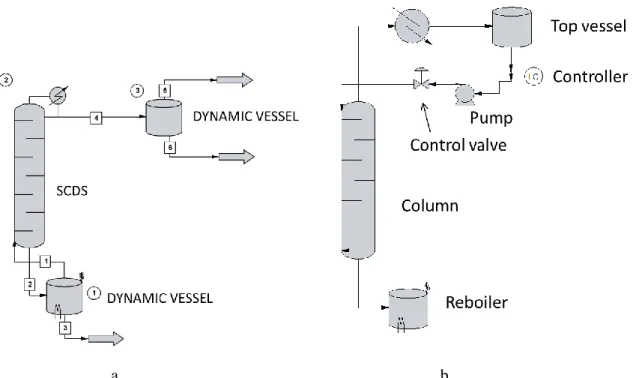
Calculation Results
- Batch Rectifier
- Middle-Vessel Column
- Comparison of the Open Mode of Batch Rectifier and of Middle-Vessel
- Comparison of the Operation Modes of The Middle-Vessel Column
- Multivessel Column
Some of the recoveries achieved with different modes of operation under different operating parameters are shown in Table 3.2. First, a comparison of the midship group and column rectifier is presented, rather than a comparison of the open and six closed midship modes of operation. However, the operation of the middle ship column is more complicated due to the higher degree of freedom.

Conclusions
Distillation path direction for different operating policies of batch heterogeneous extractive distillation. In this region of the stationary path, the retention of the E-lean phase in the decanter is reduced. The effect of continuous feeding of the entrainer on the direction of the stationary path was also studied.
The Effect of Off-Cut Recycle on the Solvent Recovery with Batch and Batch
Vapour-Liquid Equilibrium Conditions
- Pure Components and Azeotropes
- The Influence of Water on Relative Volatilities
The presence of some of the azeotropes limits the recovery of methanol, but the addition of water has a favorable effect on relative volatility. The addition of moderate amounts of water favorably changes the relative volatility of the azeotropic mixtures A-B and A-D. The increased B and decreased A concentration at the top of the column at the end of the start-up period reduces the loss of A in the precuts.
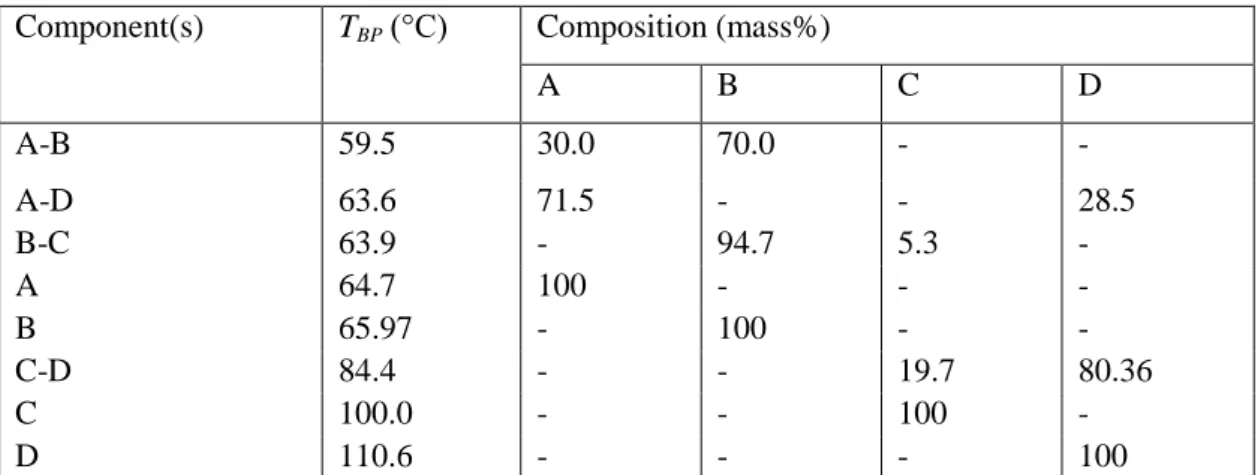
Rigorous Simulation
- Calculation Method
- Input data
- Results
- Traditional Batch Distillation
- Batch Extractive Distillation
Effect of amount of pre-cut burned on profit (in $) for methanol regeneration from batch distillation. Effect of amount of pre-cut burned on profit (in $) for batch extractive distillation methanol regeneration. Effect of the amount of pre-cut burned on the average recovery (%) of methanol.
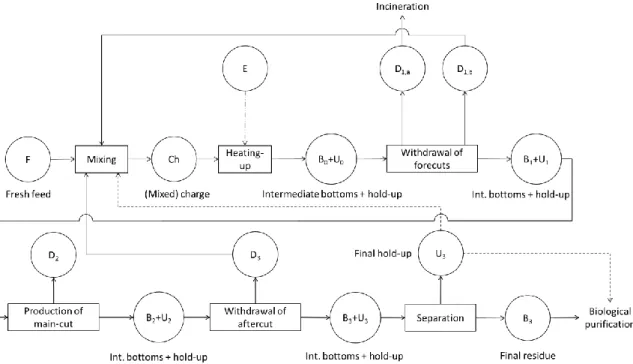
Conclusions
The loss of the main component in the precuts can be reduced with BED. The possible directions of the vectors affecting the still path of batch heterogeneous extractive distillation. The suspension of the two phases is constant and equal (125 cm3) in the decanter.
The Application of Batch Extractive Distillation for Pharmaceutical Waste Solvent
Tetrahydrofuran Recovery from a Five-Component Mixture
- Vapour-Liquid Equilibria Conditions
- VLE Data of Components and Azeotropes
- The Effect of Entrainers on the Relative Volatilities
- The Operation Modes Studied
- Experimental Part
- Preliminary Simulations
- Experimental Apparatus
- Experimental Results
- Simulation Results
- Simulation Method
- Posterior Simulation Results
- The Effect of Operational Parameters
- Comparison of Batch Extractive Distillation and Hybrid Distillation
It was possible to significantly reduce the duration of the separation process (from 310 to 168 minutes). Based on the above investigation, modifications in operational parameter values were suggested. The effect of the parameters is expressed as the relative change (in %) caused by increasing the parameter by 100.

Methanol Recovery from a Seven-Component Mixture
- Vapour-Liquid Equilibrium Conditions
- VLE Data of Components and Azeotropes
- The Influence of Water on the VLE Conditions
- Separation Methods
- Laboratory Experiments
- Batch Distillation Experiment
- BED1 Experiment
- BED2 Experiment
- Rigorous Simulation of Laboratory Experiments
- Industrial-Size Pilot Productions
- Rigorous Simulation of Industrial-Size Pilot Productions
- BD Production
- BED production
Boiling points and compositions of the four most important compounds and their azeotropes in acetone (A), methanol (B), tetrahydrofuran (C), n-hexane (D), ethanol (E), water (F). Dissolver bed fed only during column heating, then traditional correction (BED1). Steps and stopping criteria for the separation methods studied for the regeneration of methanol (B) from a mixture of waste solvents (C: THF, F: water).
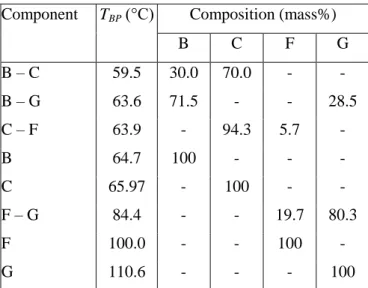
Conclusions
That is, the directions of the stationary roads are consistent with the results of the feasibility analysis. For the same reason, changing the retention of the phases in the decanter has only a small effect on the smooth path. For the same reason, changing the retention of phases in the decanter has only a small effect on the smooth path.
General Model of Batch Heteroazeotropic Distillation
Generalised Model for Feasibility Studies
L0,R and L0,W are the flow rates of the E-rich and E-poor (E-weak) phases in the condensate. The reflux split ratios rsR and rsW characterize how the flow of the E-rich and E-poor phases leaving the decanter is divided into reflux and distillate. The phase reflux ratio has a negative value, in case of reflux of the decanter hold-up from the phase to the column.
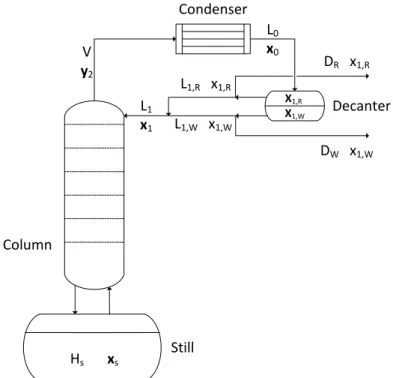
Operational Policies
- Identification of Possible Operational Policies
- The Still Path Direction of the Different Operational Policies
- Feasibility of Recovering One of the Original Components in the Still
Therefore, the direction of the resulting vector depends on the operation policy through the value of the operation parameters rR and rW. The possible directions of the derived vector, i.e. the direction of the stationary path for each possible operational policy, can be obtained by summing the above two vectors for each operational policy. The vector points towards or away from the composition of one of the phases (zones I, III, V and VII), or they are between these four cardinal directions (zones II, IV, VI and VIII).

Rigorous Simulation
- Calculation Method
- Assessment of the Practical Interest of Operational Policies
- Validation of Some New Operational Policies
- The Advantage of Using a Non-Traditional Policy
If this assumption is omitted and an average retention composition (still + column without decanter) is used instead of the still composition, the equation will have the same form. This means that the results for the quiescent path direction presented in Section 6.2 will be valid for the hold path instead of the quiescent path. At this point, instead of continuing rule 9 operation for 10 minutes, rule 15 is applied: retention of the E-rich phase is reduced (rR>1) and the E-relean phase is fully refluxed (rW =1).
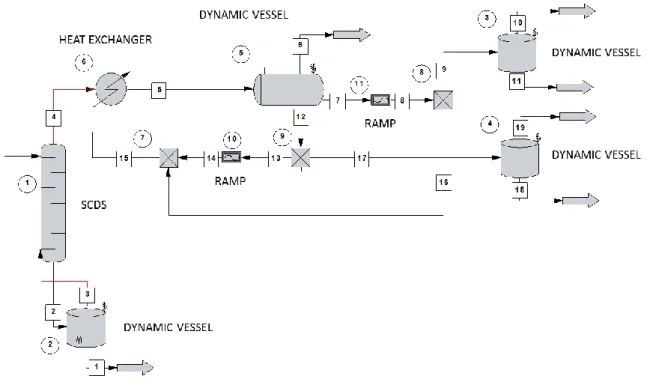
Conclusions
In this way, the operation of the decanter is directly affected by the feed of the carrier. Extraction section: the section of the column between the carrier feed and the feed (continuous distillation), or below the grass feed (batch distillation). Retention path: the trajectory of the average composition (stato+column) of the retention in the batch distillation.
The Extension of the General Model of Batch Heteroazeotropic Distillation to Batch
The Extended Model for Feasibility Studies
- Case 1
- Case 2
It can be seen that the phase split ratio of the decanter liquid is always higher than that of the condensate, and increases with the flow rate of the entrainer. In this way, the total material balance of the still (equation 6.19) has the following form: . The phase split ratio of the condensate is replaced by that of the decanting liquid, which always has a higher value.
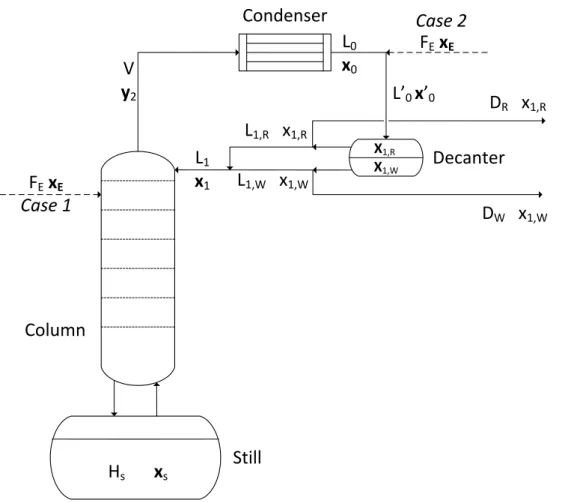
The Effect of the Continuous Entrainer Feeding
- The Possible Still Path Direction
- The Practical Significance of the Different Operational Policies
The influence of the first two terms (removal of either the E-rich or the E-lean phase) is increased, as V is replaced by V+FE. Since all the zones contain the direction of the entrainment vector, each of them overlaps other zones. Due to the reduction of the E-rich phase break in the carafe, the still path moves even faster to higher entrainer concentrations.

Rigorous Simulation
- Example 1
- Example 2
- Example 3
- Example 4
The reduction in E-rich phase retention (Policies 13-16) can be compensated for by continuous entrainer feed, which is more efficient since the latter is not limited by the initial E-rich phase retention in the decanter. The calculated (average) retention path is shown in Figure 7.5, together with the influence vectors at two different times, at the end of the run (xS,0) and at 182 min (xS,1). The only difference between this and Example 1 is that after start-up Policy 6 (partial reflux of both phases) is used: 10% of the E-rich phase and 60% of the E-lean phase are withdrawn as distillate.
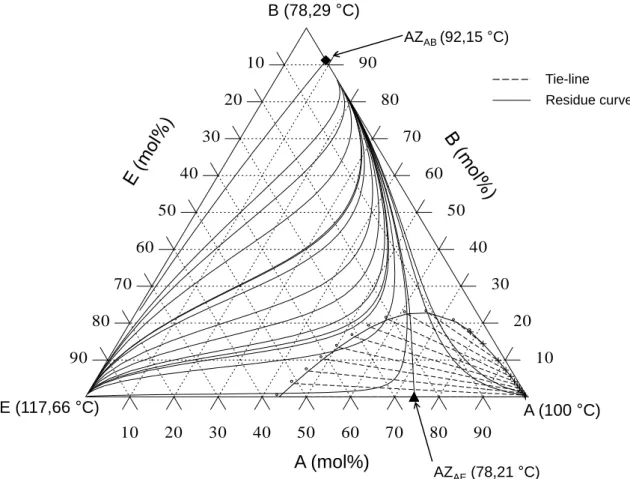
Conclusions
The present work investigates the possibilities of improving the batch distillation separation of azeotropic mixtures. In Chapter 5, the application of BED and the hybrid process (HP) was investigated for two pharmaceutical waste solvent mixtures whose separation is prevented (mixture 1: methanol, THF, acetonitrile, water, pyridine) or limited by azeotropes (mixture 2: acetone, methanol, tetrahydrofuran, n-hexane, ethanol, water and toluene). Joulia, Entrainer selection rules for separation of azeotropic and close-boiling temperature mixtures by homogeneous batch distillation process, Ind.
Supplementary Calculation Results for Chapter 3
Binary Interaction Parameters
The NRTL parameters used for the calculations presented in Chapter 6 for the water–formic acid–propyl formate and aniline–ethylene glycol–water mixtures, respectively, are given in Tables A.4 and A.5.
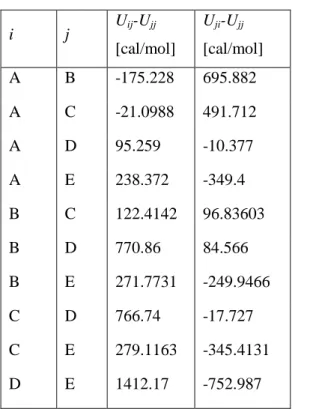
The Effect of Operational Parameters for the Regeneration of THF Using
Azeotropic composition (azeotropic point): a composition of a mixture in which the equilibrium composition of the liquid and vapor phases is identical. Homoazeotropic composition (point): a composition of a mixture in which only one liquid phase is in equilibrium with the vapor phase and the equilibrium composition of the liquid and vapor phases are identical. A stable node is not part of the stable boundary set of a stationary point.
