98 Figure 4-31 Relative humidity in the drying air medium during heat pump drying and hot air drying. 102 Figure 4-35 Energy consumption of tumble dryers with heat pump drying and hot air drying at different fan speeds.
- Sludge management in Malaysia
- Sludge handling at electroplating coating factory
- Problem statement
- Objectives
- Scope of study
- Contribution of study
The purpose of this study was to investigate the feasibility of a heat pump dryer in drying industrial sludge. Sludge samples were dried at a constant temperature (35 °C and 50 °C) using a pilot dryer with a heat pump.
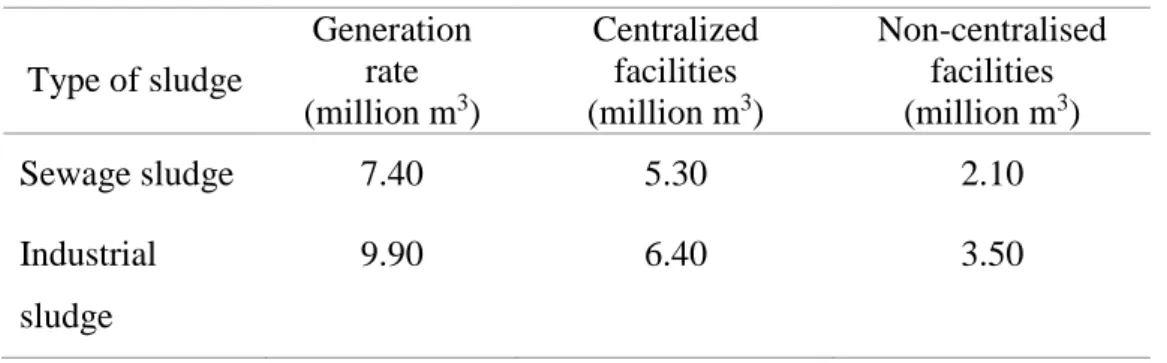
Type and characteristics of sludge
This type of mud contains metal hydroxides, which are formed during the physico-chemical processes of precipitation of metal ions in water. This type of mud contains a large amount of solid particles with a low content of associated water (eg sand, silt, slag, etc.).
Sludge treatment
If the water content of the sludge needs to be further removed, a drying process is required. Sludge drying is basically a thermal drying process where the water content in the sludge is evaporated using thermal energy.
Sludge drying
The rheological change of sludge can also influence the diffusion of moisture in the sludge and thus negatively influence the drying rate. Léonard (2010) discovered that simply pumping the sludge also influences the drying behavior of the sludge.

Sludge drying using heat pump assisted dryers
The floor of the greenhouse was heated by the second heat pump, which used waste water as a heat source. Schnotale, (2018) had reported the use of carbon dioxide (CO2) heat pump system to dry sludge.

Heat pump dryer
- Configuration of heat pump dryer
- Criteria and design consideration for a heat pump dryer
Improper design of a heat pump system can lead to inefficient operation of the heat pump dryer. EXV can increase the efficiency of the heat pump system by precisely regulating the refrigerant flow (Moon, 2003).

Sludge drying kinetic
44 The rate of drying is determined by the rate of diffusion of water through the boundary layer at the air-solid interface. Some products do not exhibit a constant rate period due to shrinkage and the surface of the product is not completely wet. 45 In the falling rate period, the surface moisture content begins to decrease, so the evaporation rate begins to decline.
In this period, the rate of drying is determined by the rate of moisture diffusion within the product. The moisture content is asymptotically approaching the equilibrium moisture content and temperature and humidity of the drying air. The basic mass and energy balance for the sludge drying process can be illustrated as in Figure 2-9.
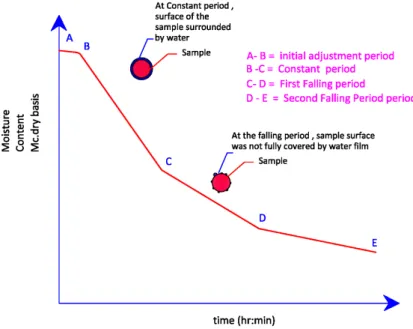
Moisture diffusivity
Assuming that the sludge has thin-plate geometry, the general solution to Equation [2.5] can be derived using In most cases, the effective diffusivity can be estimated using only the first term of the general solution (Zogzas et al, 1996). The moisture ratio MR of the sludge can be determined by the Fick's diffusion equation as follows.
- Sludge sample preparation
- Prototype heat pump dryer
- Control system of heat pump dryer
- Temperature control
- Humidity control
- Air flow control
- Process safety control
- Heat pump sizing and capacity
- Drying experiments
- Drying procedures
- Heavy metals and total organic carbon
53 Figure 3-4 shows the overall dimensions and general component layout of the pilot scale heat pump dryer. The control panel and electrical switch gears were on the right side of the heat pump dryer. At the top of the control panel was the heat pump system control section which controls the compressor and circulation fan.
A temperature controller was used to control the operation of the compressor based on the drying air temperature. A humidity controller is connected to the heat pump controller to control the operation of the compressor. In the middle of the drying room, a metal shelf was installed to hold the drying trays.
When activating the heat pump system, the circulation fan will be activated first, before other components kick in. Evaporator in the heat pump system would act as a dehumidifier, where moisture in the air would be condensed out at the cold surface of the evaporator.

Hot air drying
- Drying kinetic
- Energy performance
- Effective moisture diffusivity
This means that the drying speeds are the same for all 3 drying methods at 35 °C. However, at 50 °C, the drying kinetics in the closed mode are slightly slower than in the partially open and open modes. This may be due to the high relative humidity in the drying chamber when drying in closed mode, where the drying air has risen. Figure 4-4 Drying kinetics of the samples when drying with hot air at 35 °C at different air ratios.
Due to the accumulated moisture and high relative humidity, the drying performance in the closed state is thus reduced. Meanwhile, in the open and partially open state, the moisture-filled drying air is extracted or partially out of the drying chamber during drying. Therefore, the drying ability is not much affected, as the relative humidity is always kept at a lower level compared to that in the closed state.
77 Figure 4-10 and Figure 4-11 show the comparison of energy consumption between the drying modes at 35°C and 50°C respectively. In contrast, in partial mode and closed mode, the unused heat supply is returned to the drying chamber for the continuous drying process.
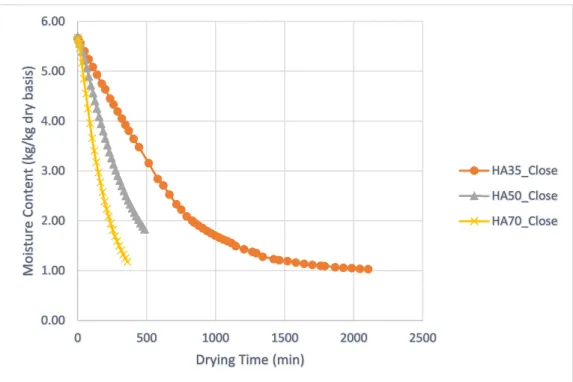
Heat pump drying
- Drying kinetic
- Effective moisture diffusivity
- Effect of relative humidity control on energy performance
- Effect of condenser type
- Effect of air flow
- Effect of bypass air ratio
- Effect of dehumidification
- Effect of heat pump compressor capacity
Moisture reduction rates for heat pump drying were always higher than for hot air drying at the same corresponding drying temperature. Therefore, for the same drying air temperature, a heat pump dryer may have a higher wet bulb depression compared to a hot air dryer. In this case, the energy consumption of the heat pump dryer was almost three times higher than that of hot air drying.
The results showed that the SMER of the heat pump dryer was much lower than that of the hot air dryer. Apparently, the relative humidity of the drying air medium in the heat pump dryer was always lower than that in hot air dryer, regardless of the fan speed. 102 Table 4-5 Effective moisture diffusion at different fan speeds for heat pump and hot air drying.
103 Figure 4-35 shows the total energy consumption of heat pump drying and hot air drying at different fan speeds. 107 Figure 4-38 shows the relative humidity of the drying air medium when drying with a heat pump at 50 °C with different circulating air ratios.

Quality analysis of dried sludge samples
According to Table 4-7, the atomic number and standard atomic mass of zinc and platinum were higher compared to other heavy metals. This made the zinc and platinum less prone to flying and depositing on the wall surface. The results showed that although drying did not thermally degrade the heavy metals in the sludge samples, the safety of flying particles should be considered, especially if the air drying medium were to be exhausted during drying.
Discharge of heavy metal particles in the drying air exhaust would then cause safety and health problems for the users. In addition, the deposition of heavy metals can cause other problems such as soiling and corrosion to the components of the dryer. Therefore, appropriate attention must be paid to the design of drying trays, airways, particle filtration and collection to reduce flying dust particles and emissions of harmful substances.

Conclusion
Compared to hot air dryer, a heat pump dryer with dehumidification capability can achieve a higher drying rate at the same drying air temperature. This was because heat pump dryer could generate drying air medium with lower humidity and therefore has a higher wet bulb depression compared to a conventional hot air dryer. On the other hand, results illustrated that SMER curves differed between heat pump dryer (concave) and hot air dryer (convex).
SMER for the hot air dryer tended to increase at the start of the drying session, while SMER for the heat pump dryer showed a downward trend from the start. The result showed that the electrical power supply for the fan in the heat pump dryer was worth it, as the higher air speed could help to improve drying speed. It could be assumed that the electricity consumption of the fan was relatively small compared to the electricity consumption of the heat pump compressor.
The results revealed that the drying kinetics were mainly governed by the condition of the drying air, regardless of the size of the heat pump compressor. Total organic carbon was not degraded during heat pump drying, but was concentrated instead.
Limitations and future works
After the drying process, the corrosive particles enter the drying air stream and cause acidic drying air that can corrode the heat pump dryer. The current pilot heat pump dryer is designed for experimental purposes that can only process about 10 kg of sludge sample. The drying experiments showed that the heat pump dryer works efficiently against the constant period, but not as efficiently as hot air drying during the decreasing period.
Therefore, continuing to use heat pump dryers during the fall period will reduce the overall efficiency of the dryer. Therefore, the next development of heat pump dryer will include programmable logic controller (PLC) to control the drying stages with different settings of drying air temperature and humidity at individual stage. The current pilot heat pump dryer with manual damper opening is difficult to control the required air flow through the dehumidification evaporator.
However, there are other hybrid heat pump dryers that can be considered to achieve additional energy savings. 2015) 'Performance analysis and modeling of a closed-loop heat pump dryer for bay leaves using artificial neural network', Applied Thermal Engineering, 87, p. 2013) Basic Refrigeration and Air Conditioning.
Since the heat transfer area A is unknown, the heat transfer coefficient is calculated based on the area of the tray, i.e. htray. Drying experiments were carried out with 3 different fan speeds to investigate the effect of air speed on drying speed. Substitute the calculated values into the Re equation, the Reynolds numbers for 30 Hz, 50 Hz and 60 Hz airflow are shown in the table (Page 138).
For turbulent flow in a rectangular passage, the Gnielinski correlation is used to calculate the heat transfer coefficient of the air flow. With turbulent flow, the Darcy friction factor can be calculated using the relationship developed by Churchill (1977), which is available in ASHRAE Handbook 2013 – Fundamental 3.7. After calculating the Nusselt number using the above correlation, then the heat transfer coefficient can be calculated as.
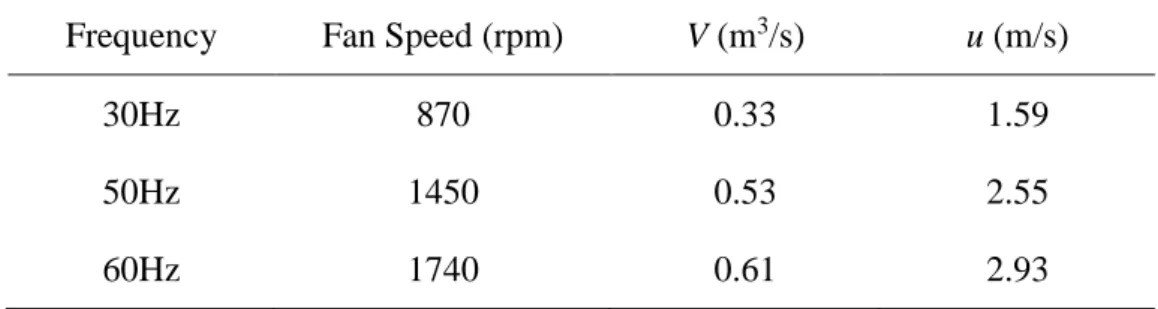
Wc = critical moisture content (kg water./kg dry solids) tc = time for constant dose period (s).