Aos meus pais, por todo o apoio, apoio e esforço dedicados a mim para que fosse possível atingir este objetivo. À ArcelorMittal Monlevade, em especial à equipe de manutenção da laminação, pela oportunidade de adquirir e aprender com experiências únicas que agregam muito à minha formação. As atividades de manutenção estão se tornando cada vez mais importantes, pois afetam diretamente a produtividade das organizações.
Diante desse cenário, torna-se necessário conhecer a fundo os equipamentos de produção para que seja possível tomar decisões assertivas, e no momento certo, sobre o tipo de manutenção a ser realizada. Para identificar o sistema a ser estudado, os tempos de parada aleatória foram estruturados de forma que fosse possível observar qual equipamento apresentava maior índice de falhas, além de analisar com a equipe responsável qual deles afetava a qualidade do produto.
INTRODUÇÃO
Justificativa
Ao identificar o nível de confiabilidade do equipamento por meio da análise do MCC, a empresa pode reduzir a ocorrência de manutenções corretivas, pois essas ações causam atrasos na produção e acarretam altos custos. Portanto, utilizar a metodologia MCC para identificar a confiabilidade dos sistemas produtivos tem como objetivo ajudar a empresa a entender, antecipar, preparar e ajustar para reduzir e até prevenir custos excessivos de manutenção corretiva. Com o objetivo de analisar a fiabilidade do equipamento estudado, de forma a obter uma maior disponibilidade do mesmo, o MCC analisa como o equipamento pode falhar e define a melhor estratégia de manutenção para prevenir avarias ou reduzir perdas por avarias (KARDEC e NASCIF) . (2012) e ROSA (2016)).
Objetivos
- Objetivo Geral
- Objetivos Específicos
Estrutura do Trabalho
REVISÃO BIBLIOGRÁFICA
- Manutenção
- Evolução da Manutenção
- Tipos de Manutenção
- Manutenção Corretiva
- Manutenção Preventiva
- Manutenção Preditiva
- Confiabilidade
- Tempo Médio Entre Falhas (MTBF)
- Manutenção Centrada em Confiabilidade (MCC)
- Distribuição de Probabilidade
- Distribuição Weibull e Weibull 3 parâmetros
- Análise FMEA
- Técnica dos 5 Porquês
Além disso, Pinto e Xavier (2001) definem os tipos de manutenção em relação à forma como são feitas as intervenções em equipamentos ou instalações, sendo as mais comuns denominadas corretiva, preventiva e preditiva. Kardec e Nascif (2009) e Papic (2009) afirmam que a incapacidade de planejar as necessidades de manutenção e prever a disponibilidade do sistema significa que a manutenção corretiva é limitada. Filho (2008) complementa afirmando que a manutenção preventiva é toda ação de manutenção e reparo realizada quando o sistema ou equipamento apresenta condições operacionais, ainda que seja uma forma de defeito.
Dhillon (2006) e Mobley, Higgins e Wikoff (2008) definem manutenção preventiva como um conjunto de técnicas preditivas, tarefas de manutenção baseadas em condição e tempo com o objetivo de cobrir toda a produção de plantas ou sistemas de produção. Segundo Filho (2008) e Marçal (2000), as atividades de manutenção programada compreendem o monitoramento ou acompanhamento do estado dos equipamentos, seja por desgaste ou eficiência operacional, realizada por meio de medições ou inspeções que não perturbem o funcionamento do sistema. Papič (2009) afirma que os componentes ou sistemas apresentam alguns sintomas antes de falharem e que a manutenção preditiva pode determinar o estado em que a máquina está operando e determinar se ela precisa de manutenção.
Segundo Raposo (2004), a manutenção preditiva tem duas abordagens, na primeira é tratada como uma modalidade de manutenção dentro da manutenção preventiva onde não se conhece a degradação do sistema e se faz um monitoramento contínuo dos parâmetros. Na segunda abordagem, as técnicas de manutenção preditiva são tratadas como uma evolução da manutenção preventiva sistemática, que é considerada uma forma de manutenção. Wireman (1998), diz que o MCC é uma evolução da manutenção tradicional cujo principal objetivo é focar nas funções mais importantes do sistema, reduzir as tarefas de manutenção e também reduzir os custos de manutenção.
Com base nessas expectativas, o MCC é uma metodologia que, quando aplicada, permite que uma organização gerencie melhor suas atividades de manutenção, podendo atuar nos pontos mais críticos de seu processo e, assim, reduzir esforços desnecessários por meio de atividades de manutenção corretiva. , pois com essa metodologia a equipe gestora pode direcionar qual tipo de manutenção é mais viável para determinado sistema ou equipamento. Segundo Smith e Hinchcliffe (2004), o MCC foi desenvolvido devido à necessidade de desenvolver uma estratégia de manutenção planejada que focasse na disponibilidade e segurança do sistema sem aumentar os custos. Esses resultados esperados mostram como a implementação do MCC pode trazer benefícios para a organização ao identificar e focar os esforços da equipe de manutenção no centro do problema e evitar o investimento desnecessário de esforço quando não é necessário.
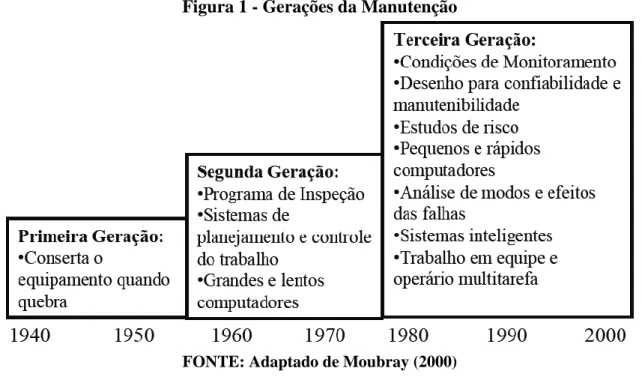
METODOLOGIA DE PESQUISA
Classificação da Pesquisa
Coleta e Análise dos Dados
DESCRIÇÃO DO PROBLEMA
Apresentação da Empresa
Descrição do Laminador 2
Nesta etapa, a haste é direcionada para a via Stelmor, caso se queira obter um fio-máquina com bitola menor, ou para a via Garret, caso se deseje obter um fio-máquina com bitola maior. Ao final desse processo, ocorre a formação das espirais e o processo de resfriamento, que chega até o processo de formação das bobinas, para que sejam enviadas ao processo de manuseio, que irá compactar, rotular e embalar as bobinas para que sejam encaminhados ao setor de logística e encaminhados aos clientes. A Figura 2 mostra o layout da Laminação 2, onde é possível observar os processos desde a entrada do tarugo até a saída do fio-máquina em forma de bobina.
Descrição do Problema
DESENVOLVIMENTO
- Identificação e Seleção do Sistema Crítico a ser Tratado
- Coleta e tratamento dos Dados de Paradas Acidentais
- Análise dos Dados de Confiabilidade
- Gráfico Função Densidade de Probabilidade (PDF)
- Gráfico de Probabilidade Weibull 3 Parâmetros
- Gráfico Função de Sobrevivência
- Gráfico Função de Risco
- Elaboração do FMEA
A preferência por priorizar o sistema B em detrimento do sistema A neste estudo se dá pela importância deste sistema para a qualidade do produto, pois o sistema a ser estudado tem contato direto com o produto e qualquer modo de falha presente pode degradar e até mesmo descartar o produto. A partir dos valores dos 3 parâmetros, foram gerados gráficos no Minitab17 que possibilitaram identificar a confiabilidade do componente em relação ao tempo trabalhado, conforme pode ser observado nas Figuras 12, 13 e 14. Ex. Aproximadamente. 5% dos componentes apresentarão algum tipo de falha durante 150 horas de trabalho (Figura 11).
Ao contrário do que pode ser visto no gráfico da função de sobrevivência, o gráfico da função de risco (Figura 11) mostra que o risco de fratura do componente aumenta com o tempo de operação. Ao usar o eixo y para comparar as taxas de falha para itens de sobrevivência com o tempo dado no eixo x, uma comparação pode ser feita levando em consideração o tempo de operação do item. Por exemplo, um componente que operou perfeitamente por 250 horas tem uma função de taxa de falha de aproximadamente 0,003, enquanto um componente que operou sem falhas por 700 horas tem uma função de taxa de falha de aproximadamente 0,006.
Para identificar os principais erros característicos do componente crítico, a equipe responsável pela aplicação da metodologia desenvolveu um FMEA para dar uma visão geral melhor da funcionalidade do equipamento e o que pode acontecer em caso de falha. Além das causas fundamentais dos modos de falha conhecidos pela experiência dos envolvidos, seja obtida por meio de documentos sobre o componente ou por experiências vividas durante o tempo de trabalho. Em um segundo momento, já de posse das possíveis falhas funcionais, elencaram-se, conforme entrevistas com os responsáveis pelo sistema e com os dados encontrados no sistema MES, os possíveis modos de falha para causar falhas funcionais, ou seja, se Se ocorrer um erro funcional, ao chegar na área do sistema onde o componente está localizado, “quais modos de falha você consegue visualizar rapidamente?”.
Uma vez identificados os modos de falha, foi gerado o Número de Prioridade de Risco (RPN) onde o valor atribuído às colunas foi multiplicado em relação à gravidade, ocorrência e detectabilidade do modo de falha, para tais colunas são usados valores de 1 atribuídos a 10 , onde o valor da coluna de gravidade é atribuído em ordem crescente, ou seja, quanto mais crítico, maior o valor, na coluna de eventos, quanto mais frequentes os eventos, maior o valor a ser atribuído à coluna , e , na coluna de detectabilidade, quanto maior a probabilidade de detecção da falha, menor o valor a atribuir à coluna. Após identificar os possíveis modos de falha e gerar seus respectivos RPNs, aplicou-se a técnica dos “5 porquês” aos modos, para que fosse possível entender a fundo o que realmente poderia causar tais modos de falha. Aplicando o MCC, utilizando o FMEA e a técnica dos “5 porquês” e com o resultado obtido em relação ao tempo de paradas não intencionais, pode-se constatar que houve um aumento na confiabilidade da peça estudada, ou seja, houve seria um aumento no MTBF, o que deslocaria as curvas dos gráficos de sobrevivência e risco para a direita, de forma que 90% dos componentes teriam qualidade aceitável mesmo após mais de 125 horas de operação, conforme o gráfico de função de risco a componente teria uma taxa de falha de aproximadamente 0,003 após 250 horas de operação.
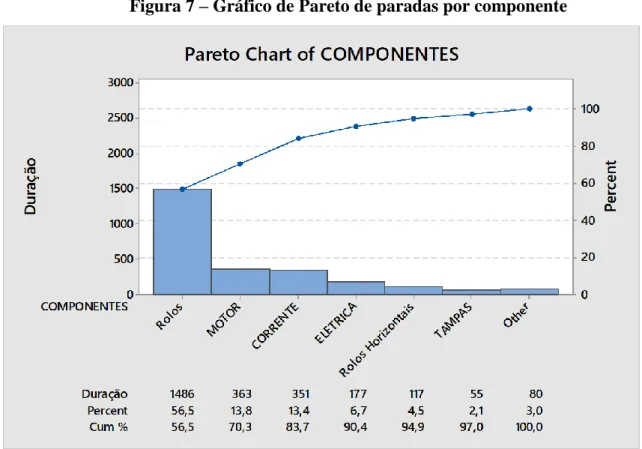
CONSIDERAÇÕES FINAIS
No final do processo de implementação da metodologia, foram desenvolvidas medidas de mitigação dos modos de falha que permitiram à organização alterar os planos de inspeção e alterações no sistema, alterações que trouxeram ganhos à organização, tanto em produtividade como em fiabilidade, que é o objetivo principal. de desenvolvimento do trabalho. Assim, podemos concluir que as atividades para um sistema confiável são de extrema importância não só no planejamento da produção e manutenção, mas também no planejamento estratégico de toda a organização, pois é possível obter vantagens competitivas com esta confiabilidade. Portanto, com o desenvolvimento deste trabalho, fica evidente a importância de entender o funcionamento de todo o sistema, bem como seus possíveis erros, a fim de possibilitar a adoção de decisões assertivas que gerem cada vez mais benefícios para a organização.
Como sugestões para trabalhos futuros, continuar monitorando os equipamentos em estudo e aumentar a abrangência do sistema, reduzindo ainda mais o tempo gasto em paradas acidentais. Gerenciando a introdução da Manutenção Centrada em Confiabilidade, RCM – RCM como método de trabalho nas organizações hidrelétricas. Tese (graduação) – Departamento de Negócios e Ciências Sociais – Departamento de Qualidade e Gestão Ambiental, Luleå University of Technology.
A case study of application of Reliability Centered Maintenance (RCM) in Advanced Amphibious Assault Vehicle (AAAV) acquisition. An Introduction to the US Naval Air Systems Command's RCM Process and Integrated Reliability Centered Maintenance Software.