Análise e melhoria da produtividade numa empresa do sector de componentes de automóveis
Texto
Imagem
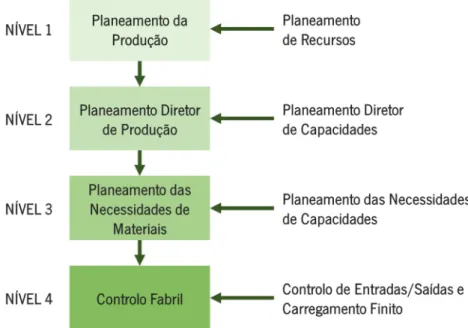

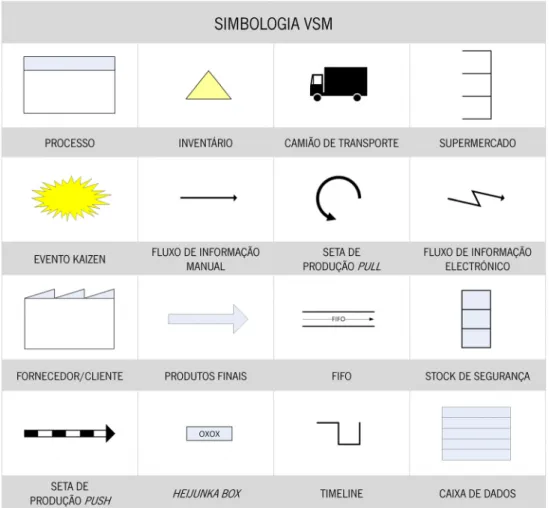

Documentos relacionados
Foram encontradas, também, as pes- quisas de Soares (2007), sob o título “O Sistema Nacional de Avaliação da Educa- ção Superior e a Gestão Estratégica das
insights into the effects of small obstacles on riverine habitat and fish community structure of two Iberian streams with different levels of impact from the
There a case in Brazil, in an appeal judged by the 36ª Câmara Cível do Tribunal de Justiça do Estado de São Paulo (São Paulo’s Civil Tribunal, 36th Chamber), recognized
Neste estágio, assisti a diversas consultas de cariz mais subespecializado, como as que elenquei anteriormente, bem como Imunoalergologia e Pneumologia; frequentei o berçário
O fortalecimento da escola pública requer a criação de uma cultura de participação para todos os seus segmentos, e a melhoria das condições efetivas para
Então são coisas que a gente vai fazendo, mas vai conversando também, sobre a importância, a gente sempre tem conversas com o grupo, quando a gente sempre faz
Neste capítulo foram descritas: a composição e a abrangência da Rede Estadual de Ensino do Estado do Rio de Janeiro; o Programa Estadual de Educação e em especial as
de professores, contudo, os resultados encontrados dão conta de que este aspecto constitui-se em preocupação para gestores de escola e da sede da SEduc/AM, em