The development has been purposefully achieved by using automation in the production system with the right scope to improve the company's performance. The focus for development in the system is on a soldering process, which is the most used operation in the company. It was the bottleneck in the system and consequently limited the company's performance.
The goal of the project is to improve the customer's production system by using automation in its system. A detailed design of the entire project is made and a new layout for the system is outlined. Next, the progress of the project is reported and the challenges it encountered are analysed.
Safety and ergonomics for the human workers may also be low if the system is under-automated. The appropriate level of automation, also called "rightomation", can be achieved with a careful study of the production system. The Rightomation indicator can be found at the highest point of the curve and indicates the right level of automation for the system.
When the level of output per hour of labor input increases, the productivity of the system is improved.

3 BRAZING
Before choosing a brazing method, the properties of the composite metals and the filler metal used must be observed. When choosing a fuel gas, the required temperature and the cost of the process are usually the most important. Immersion soldering is one of the soldering methods and it is performed by immersing the metals in a heated bath.
The assembled parts are held together in the heated bath, and when the assembly reaches the temperature of the bath, bond metal flows into the assembly. The brazing method chosen must be suitable for the metals being joined, and the properties of the base metals must be carefully examined to avoid quality defects. If the properties of base metals differ significantly, thermal expansion can cause reactions in the metals that degrade quality and strength.
In addition, if a flux is used in the process, it must be suitable for all metals and the temperature of the filler metal. To create a strong connection, a suitable shape of the connection must be designed. It is also important to be aware of the possible changes in joint size as the parts expand when heated.
The most common assemblies can be classified into two different categories, depending on the placement of the pieces. When the ends of the pieces are attached by soldering, the joint is called a butt joint. In a lap joint, the surfaces of the pieces are attached instead of the ends, resulting in a larger joint area.
A good joint is uniform and leak-proof and its strength is equal to or greater than that of the base metals. A brazed joint also retains many metallurgical properties of metals because no melting of the base metal occurs. That's because softer filler metals are preferred when brazing, which affects the final strength of the joint.

4 PROFITABLE MANUFACTURING
Just-in-time (JIT) is one of the tools of lean and it is an idea to produce what is needed exactly at the right time and not more in quantity than is needed. Therefore, only standardized products are suitable for make-to-stock and the demand of the products should be probable. A company using an assemble-to-order strategy has the basic parts of the product manufactured and stored in inventory, which are later assembled to order.
The need for an inventory generally depends on the stability of demand when considering a company's products. Demand may vary seasonally or occasionally and being aware of the variation is essential when designing stock. However, this presupposes a short lead time of the product in order to bring them to the market on time.
The characteristics of the product and the variation in its demand mainly define the most suitable option for each company. In general, the correct level of automation depends on the variety and volume of products produced, and a guideline for finding the appropriate level is illustrated in Figure 4 below. The technological level therefore depends on the variety and volume of production.
A flexible system focuses on the end customer and has a fast throughput of the products that meet the customers' needs. If the predictability of the variation in demand is high, the product range can be small and the inventory kept low. On the contrary, when the variation in demand is difficult to predict, the system faces challenges in meeting the requirements of the customer.
If the level of production units in the system is high, the development of the production system can be a challenge, because these unfinished products hide the problems of the system. To create a production process with short lead times and low WIP inventory, the layout type must match the volume and variety of products produced. The type of layout chosen has a tremendous impact on the flow time and flow of the production system.
Errors and challenges in the functioning of the product must be recognized and developed to solve the problem. Do phase contains the testing of the hypothesis and the results are examined in the Control phase.

5 DEVELOPMENT PROJECT
The actual solder occupies the smallest area and is placed in the corner of the system because of the heat it produces. The performance of the new system is then evaluated using a measurement chart designed for the project. Different parameters, such as lead time, productivity and duration of the process, are examined in the chart before starting the project.
Before starting to redesign the manufacturing system, the old system had to be carefully examined. Soldering is the only job of the second employee and is marked in yellow in the figure. Automating soldering is quite simple and inexpensive and fits within the customer's budget.
In this setup, the mounting operation is located at the beginning of the system and is performed on wheeled tables. At the end of the conveyor belt, the carriers slide down the slope to the table, where they cool down for a suitable amount of time. Its length depends on the efficiency of the torch, and the stronger the torch, the faster the soldering.
The slope and table at the bottom of the conveyor must withstand high temperatures as they hold the hot bearings. Factors influencing the success of the project are being carefully examined in the chart. Project success is in the middle of the chart as it is the main perspective of the project.
The company valued the quality of the system the most, as the production system is aimed at operating as efficiently as possible. The price of the project is also an important factor, since the company is quite new and small. After the creation of the implementation project, the continuation according to the project plan began.
The purpose of the test brazing was to measure the time required for the torch to melt the filler metal. Due to the properties of the filler metal and the heat absorbing tendency of the support, the torch was unable to sufficiently heat the assembly in the test weld.

6 EVALUATION OF THE PROJECT
If the system had been developed based on the properties of the old filler metals, the system might not function perfectly with the new ones. They allowed a delay in the project to ensure premium quality of the new system. If the heat absorption tendency of the support material had been reported early in the development phase, material and time would have been saved.
The quality of the system was assessed as agreed during the project, so the fact that the final completion of the new system is delayed for some time is not a big problem. The new filler metals will most likely improve the quality of the products and enable the eventual automation of the soldering operation. In addition, releasing one employee to improve products and systems allows for further development of the company and its products.
A clear understanding of the upcoming phases should be explored as the first goal of the project has not yet been achieved. After receiving the conveyor, the next step is to install the components of the system and mount the placement stations. To get a good picture of the company's condition and competitive position, a SWOT analysis has been made based on the current situation.
SWOT analysis is a tool that helps to gain awareness of the strengths, weaknesses, opportunities and threats that a company experiences. Strengths and weaknesses focus on the internal situation of the company while opportunities and threats represent external factors, focusing on the future (Kamensky 2000. 172). The strengths and weaknesses in the analysis describe the current situation of the company and help to find things that need to be evaluated and paid attention to.
Opportunities and threats are considered both from the company's side and from the perspective of the new system's introduction. It is an advantage to be prepared for the challenges that the new system may bring, and to be aware of the opportunities it may provide. The best use of the new system can be achieved with careful preparation and quick responses to challenges throughout the project.
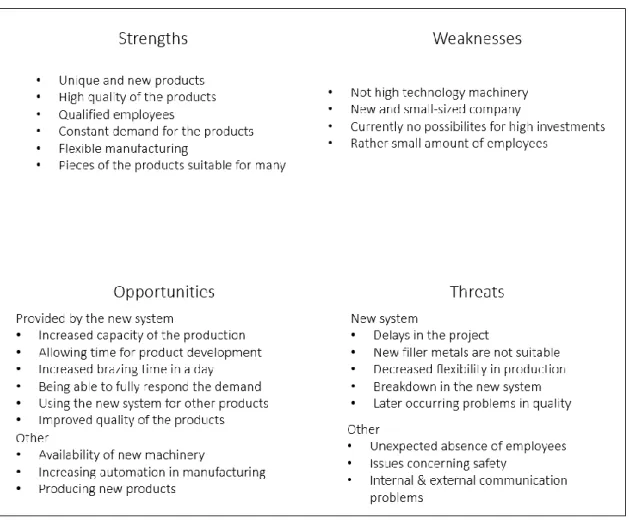
Measurement chart
System chart