APLICAÇÃO DE FERRAMENTAS DE CONTROLE ESTATÍSTICO DE QUALIDADE PARA REDUZIR O DOWNTIME NO. Trabalho de conclusão de curso oferecido como requisito parcial para obtenção do título de Engenheiro de Produção pela Universidade Federal de Ouro Preto. O presente trabalho oferece, portanto, uma proposta de utilização de ferramentas estatísticas e de controle de qualidade na análise do tempo em que a laminação de uma indústria siderúrgica é parada, a fim de maximizar o indicador de produtividade.
Portanto, este estudo apresenta uma proposta de utilização de ferramentas de controle estatístico e qualidade na análise do tempo ocioso de uma laminadora de uma indústria siderúrgica para maximizar seu indicador de produtividade. Ferramentas estatísticas de controle de qualidade foram usadas para identificar falhas e indicar melhorias no desempenho da fábrica.
Pergunta Problema
A busca por tais melhorias pode ser realizada por meio de métodos estatísticos de controle de processos e ferramentas de gestão da qualidade.
Justificativa
Objetivos
Objetivos Gerais
Objetivos Específicos
Estrutura do Trabalho
Assim, este estudo justifica-se pela necessidade de maximizar a produtividade e otimizar a utilização dos recursos de forma a garantir uma redução dos custos operacionais e uma vantagem competitiva no mercado. Esta seção fornece uma explicação passo a passo de como conduzir a pesquisa, desde a coleta de dados, passando pela análise e interpretação, até a proposta de melhoria e conclusão. Na quarta parte, o problema de pesquisa é confirmado e uma análise estatística é realizada em busca das causas do problema.
Após destacar o problema e suas causas, a quinta seção propõe melhorias no processo de torneamento a fim de reduzir o tempo de parada e aumentar a produtividade.
Siderurgia
Laminação
Processos
Controle de Processos
Ferramentas de Controle Estatístico
- Gráfico de Pareto
- Diagrama de Causa e Efeito
- Análise de Regressão
- Análise de Variância (ANOVA)
- Comparações Múltiplas de Médias
A análise de regressão é um modelo que pode ser utilizado para investigar a relação entre as variáveis envolvidas em um determinado processo. Na análise de regressão simples, apenas uma variável de regressão está relacionada à variável de resposta; e a regressão múltipla correlaciona a variável resposta com mais de um regressor. Segundo Montgomery (2009) apud (PAESE et al., 2001), a análise de variância, também conhecida como ANOVA, é uma ferramenta para comparar diferentes grupos ou estratos de interesse.
Montgomery (2009) interpreta o resultado da seguinte forma: se a hipótese nula for aceita, cada observação é formada pela média global μ mais o erro aleatório Єij. SQT = SQTreatments + SQE (6) Assim, Montgomery (2009) mostra que a variabilidade total presente nos dados SQT pode ser dividida entre a soma dos quadrados das diferenças entre a média do tratamento e a média global (SQTreatments) e a soma dos os quadrados das diferenças entre as observações de um tratamento e a média dos tratamentos. Ainda segundo Montgomery (2009), a existência de diferenças entre as médias observadas nos tratamentos e a média global mede as diferenças entre os tratamentos; as diferenças entre as observações dentro de um único tratamento e a média dos tratamentos são atribuídas ao erro aleatório.
Montgomery (2009) também chama a atenção para um fator importante na realização de uma análise de variância: a distribuição em número de graus de liberdade, que corresponde à identidade da soma dos quadrados. Considerando que existem níveis do fator, temos SQTreatments com a-1 grau de liberdade. MQTreatment = SQTreatment/(a – 1) (7) Assim, se a hipótese nula H0 for verdadeira, MQTreatment torna-se um indicador imparcial de σ2.
É claro que o erro quadrático médio MQE é um estimador imparcial de σ2 independentemente de H0 ser aceito ou não. Entretanto, quando a hipótese nula é rejeitada e a hipótese alternativa (de que as médias não são iguais) é aceita, ainda não se sabe quais entre as médias da população são iguais e quais são diferentes (WALPOLE, 2009). O Diagrama de Causa e Efeito explicado no item 2.4.2 é amplamente utilizado na elaboração de um plano de ação.
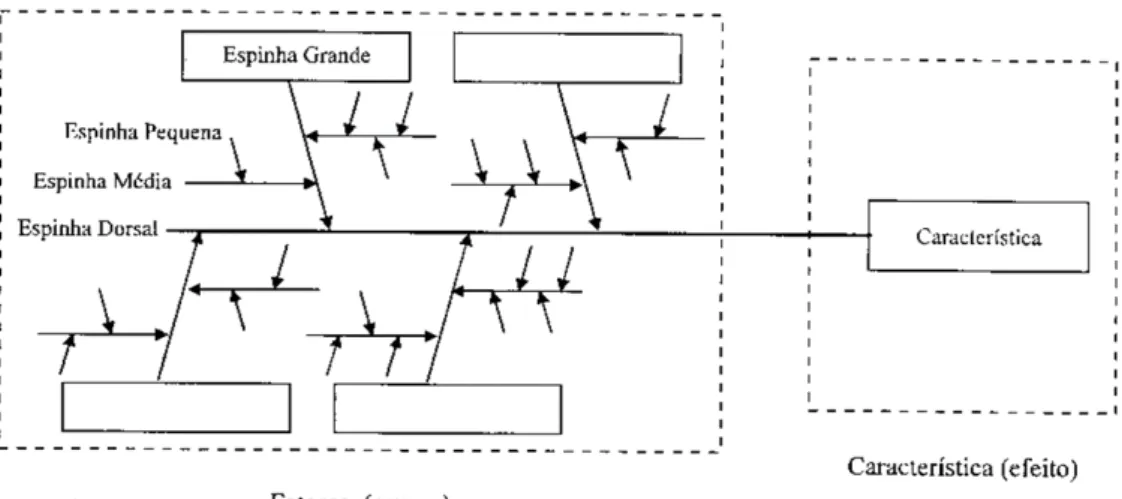
Classificação da Pesquisa
Coleta e Extração de Dados
Apresentação da Empresa
Descrição do Laminador 2
Em seguida, já no processo C, o tarugo aquecido entra nas cadeiras de laminação, onde a barra de aço sofre alongamento e redução de espessura. Após o estiramento, o material segue para o processo D, podendo passar para a linha Garret (bitola pesada) ou Stelmor (calibre fina). No processo via Stelmor, o material sofre diversas deformações até atingir a espessura desejada, transformando-o em espiral.
Feito isso, inicia-se a fase de resfriamento do material, ainda no processo D, primeiro por tanques de água e, posteriormente, por ar.
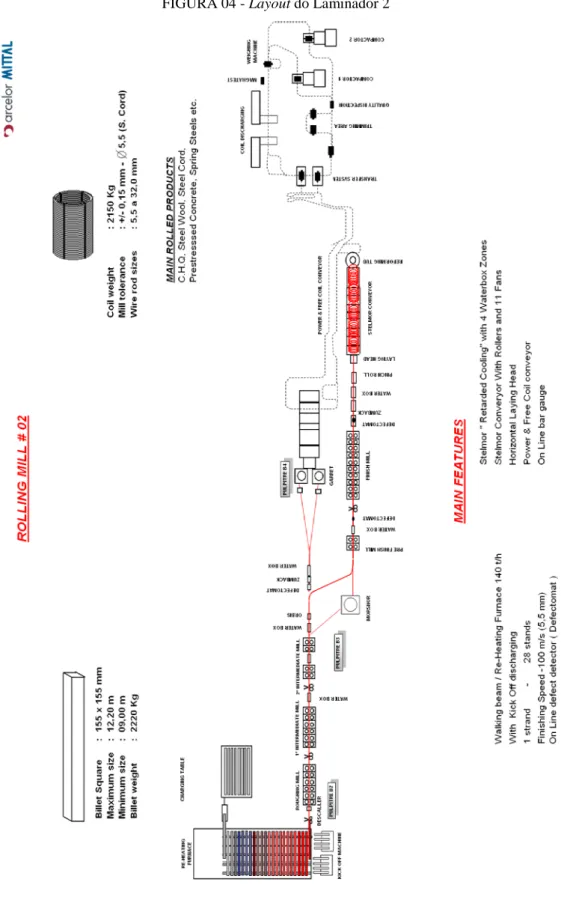
Indicadores de Desempenho do Laminador 2
- Produtividade
- Taxa de Utilização
- Eficiência
- Tempo de Parada
Durante a produção diária de fio-máquina, o laminador para por diversas ocorrências. Tais fenômenos são chamados de paradas e são divididos em três categorias, a saber: paradas planejadas, paradas acidentais e paradas logísticas. Cada uma dessas categorias é dividida de acordo com a origem da ocorrência que gerou o banimento, para facilitar o controle das taxas de banimento.
Todos os processos de laminação estão sujeitos a proibições de todas as categorias e o controle do registro das proibições de laminação, para cada origem, é crucial para aumentar a produtividade. Funcional: o tempo em que o Laminador fica parado devido a falhas, avarias ou problemas de qualidade por motivos funcionais;. Externo: momento em que o laminador fica parado por motivos externos ao laminador ou à fábrica, como falta de energia ou mau tempo.
O tempo em que o laminador fica parado devido a atividades logísticas necessárias para a produção, como troca de linha de produção e equipamentos. As paradas logísticas são necessárias de acordo com o cronograma de produção, que é determinado de acordo com a carteira de pedidos.
Descrição do Problema
Significado das Origens de Parada
Portanto, é necessário determinar quais fontes extrapolam mais significativamente sua meta para contribuir de forma mais intensa com as paradas da linha de produção. Para entender a contribuição real de cada fonte para o tempo de inatividade total, foi calculada a porcentagem pela qual cada uma das médias difere das metas. Nota-se que as fontes elétricas e programadas representaram uma percentagem negativa acima da meta, o que significa que tais fontes tiveram em conta a meta pretendida e não têm impacto devido ao número total de paragens estar acima do previsto.
Para determinar o impacto de cada um dos recursos restantes no problema de "tempo de inatividade total", foi criado um gráfico de Pareto mostrando o número de minutos em que os recursos excederam suas metas. Analisando o gráfico, podemos concluir que as falhas mecânicas e logísticas são responsáveis por 80% das falhas acima da meta. Para demonstrar a importância das paradas mecânicas e logísticas como as principais causas de paradas maiores que as planejadas que ameaçam o índice de produtividade, foi realizada uma análise de regressão comparando a relação entre o percentual de parada e a quantidade de fio produzida pela máquina.
Primeiro, usamos dados de todas as fontes ao longo dos doze meses de 2014 e a produção em cada um desses meses. A Tabela 04 mostra o resultado da análise de regressão correlacionando todos os percentuais da origem da sucata com relação à produção de arame laminado. A Tabela 05 contém dados e uma análise de regressão que relaciona a produção apenas com o percentual de paradas mecânicas e logísticas.
Analisando os coeficientes de correlação estabelecidos, percebe-se que os índices de correlação ao comparar a variável de produção com todas as variáveis de parada e comparando apenas as variáveis mais críticas são praticamente os mesmos. Embora esta pesquisa tenha demonstrado a importância das paradas logísticas para o tempo de inatividade total, este trabalho focou apenas nas paradas mecânicas, pois o alto índice de paradas logísticas se justifica pela necessidade de atender carteiras de pedidos que variam muito do estado atual. condições de mercado. Por outro lado, os encravamentos mecânicos não estão previstos e são de origem aleatória, pelo que todos os esforços devem ser contidos.
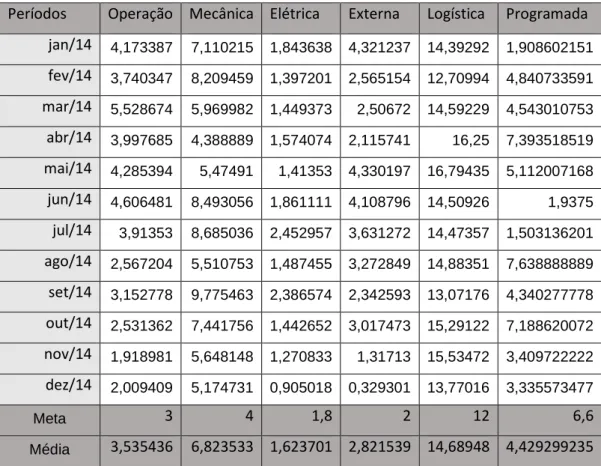
Paradas Mecânicas
Por meio do gráfico de Pareto é possível identificar os principais tipos de batentes de origem mecânica, bem como os equipamentos que os compõem. Desta forma, foi realizada uma análise das proibições mecânicas dos processos de laminação e segundo grupos de trabalhadores. Para identificar qual processo tem o número mais crítico de interrupções, foi realizada uma Análise de Variância em nível de significância comparando os tempos médios sem produto dos quatro processos de fiação.
A Tabela 09 mostra a comparação do tempo médio de parada por processo, realizada por meio do teste de Tukey. É importante acompanhar o número de paradas por grupo, para saber se algum deles contribui mais significativamente do que os outros para o tempo total de paradas. A Tabela 10 mostra os minutos de parada para cada uma das quatro turmas de janeiro a dezembro de 2014.
Pela análise da tabela, determina-se que os Transportadores 1 a 5, Stelmor e Turntable, e No Twist serão as prioridades na proposição de soluções, visto que têm uma contribuição mais significativa em minutos para o total de paradas mecânicas e estão em processos que são comprovadamente mais críticos para a laminação. O forno, por outro lado, é priorizado como nível 3 porque sua contribuição para o tempo de parada é menos significativa e porque é uma parte do processo que se mostrou menos importante para o tempo de parada mecânica geral. Em termos de processos, existem os processos E (Manipulação), D (Stelmor) e C (Laminação) com prioridade 1, pelo facto de todos possuírem equipamentos que contribuem significativamente para o desperdício total; a adequação desses processos também foi verificada juntamente com o tempo de paradas mecânicas na atividade de laminação.
Para verificar os principais motivos pelos quais o número de paradas mecânicas é alto, foi utilizado o diagrama de causa e efeito. Cada uma das causas levantadas no diagrama de causa e efeito foi descoberta, alimentando seis tabelas que organizam as ações de um plano que visa reduzir o número de paradas mecânicas na Laminadora. Além disso, procurou-se verificar qual processo de atividade rotacional e qual grupo de operadores mais contribuiu para a ruptura mecânica.
Diante disso, foi realizada uma Análise de Variância para comparar as paradas médias entre processos e classes. Nesta etapa, um Diagrama de Causa e Efeito foi utilizado para determinar as causas de paradas mecânicas acima do esperado.
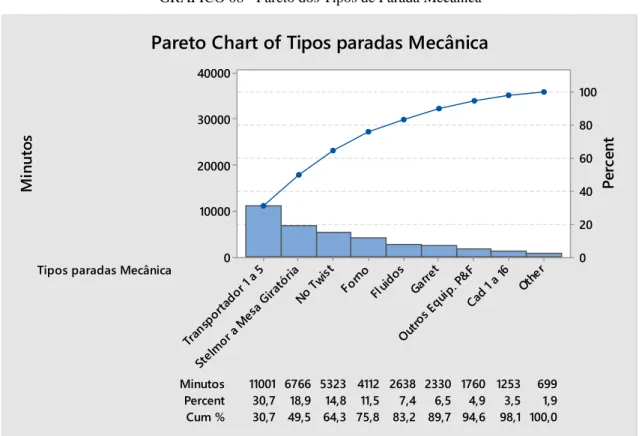
Sugestões para Trabalhos Futuros