47 Figura 4.12 Perfil de aquecimento e resfriamento usado no modelo de três barras para simulações de tensões residuais. Figura 5.9 Estado final de tensões no modelo de três barras para o material modelo P1150, com aumento de deformação de 10x. a) Vista frontal; b) Vista lateral direita;. 61 Figura 5.14 Comparação entre os perfis de temperatura dos modelos de calibração da fonte de calor e do modelo de placas.
Objetivo Geral
Objetivos Específicos
Aços ARBL
Como pode ser visto, a maioria dessas aplicações envolve o uso de componentes de soldagem, que introduzem tensões residuais no material. Desta forma, a necessidade de compreender é clara. as tensões residuais decorrentes do procedimento de soldagem e suas interações com a transformação martensítica.
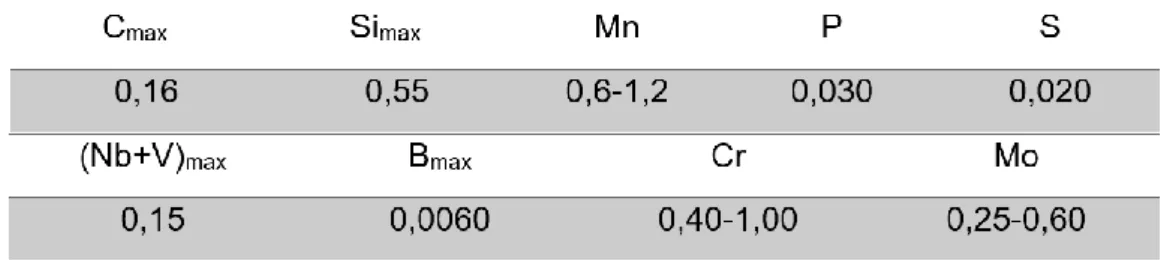
Métodos Numéricos
A Figura 3.4 apresenta a mesma geometria ilustrada na Figura 3.2, porém com uma malha de elementos mais refinada, com maior número de nós. A Figura 3.7 apresenta esquematicamente as principais considerações utilizadas na literatura para a resolução de simulações de soldagem.

Analise térmica
- Distribuição Gaussiana
- Duplo elipsoide de Goldak
- Calor especifico e calor latente
- Condutividade térmica
- Endurecimento isotrópico bilinear
- Coeficiente de expansão térmica e temperatura de início da
Este modelo assume a forma de uma combinação de dois elipsóides, descritos pelas equações 3.7 e 3.8, e representados pela Figura 3.10. As dimensões da fonte de calor devem ser ajustadas levando em consideração o perfil da zona de fusão. O resultado obtido pelo grupo pode ser visto na figura 3.11, que mostra o resultado do modelo ajustado para as telhas 3; 4; 5 e 6 mm de espessura, considerando uma entrada de calor de 240 J/mm através da soldagem GTAW.
Como referência para calibrar o modelo matemático baseado no elipsóide duplo de Goldak, Xu et al. 2012), utilizou nove termopares localizados próximos ao cordão de solda depositado por soldagem GTAW em uma chapa de aço AISI/ABNT 316L, cujas posições podem ser vistas na Figura 3.12. Com base em uma ferramenta de ajuste iterativo de fonte de calor (HSF), presente no software Sysweld, aplicada a um modelo bidimensional da placa (Figura 3.13) e os sinais coletados por termopares, Xu et al. 2012) chegaram a um modelo térmico apresentado pela Figura 3.14. A Figura 3.15 ilustra uma comparação entre as temperaturas calculadas pela simulação e as medidas pelos termopares em suas respectivas posições, e mostra a calibração do modelo.
A Figura 3.20 mostra o modelo de endurecimento isotrópico bilinear aplicado por Haibatollahi e Tehrani (2013) em seu estudo. Os modelos de materiais utilizados nas simulações de tensões residuais foram baseados no modelo apresentado por Porcaro (2019), cujas propriedades termomecânicas podem ser vistas na Figura 3.23.

Material
Simulações do modelo térmico pelo Método dos Elementos Finitos
Para as simulações numéricas foi utilizado o pacote de software Ansys 2021 R1, a Figura 4.1 apresenta um fluxograma para as etapas planejadas. A montagem final pode ser vista na Figura 4.5, os detalhes da aquisição da temperatura são apresentados na próxima seção. Assim, optou-se por utilizar o modelo de fonte de calor gaussiana bidimensional, devido a sua facilidade de uso e pequena diferença de resultados em relação ao modelo de Goldak.
A implementação da fonte de calor foi realizada utilizando o trecho de código APDL (Ansys Parametric Design Language) no ambiente Ansys Mechanical©, mostrado na Figura 4.8. Aqui, pode-se observar a presença de três variáveis principais que devem ser inseridas no código: X equivalente à velocidade da fonte de calor; Y refere-se ao termo 2𝑠2 presente na equação 3.5; e Z o resultado da equação 3.6. A calibração da fonte de calor foi realizada utilizando a geometria mostrada na Figura 4.9, criada com o programa SpaceClaim CAD (Computer Aided Design) presente na suíte Ansys 2021 R1.
Neste modelo, o cordão de solda fica no centro da chapa, no sentido longitudinal, e inicia-se a fonte de calor. Após estudos de convergência do modelo térmico, refinamentos e análise dos resultados finais para diferentes malhas, o observado na Figura 4.10 foi definido apenas como o modelo final para calibração da fonte térmica, com 11760 elementos e aproximadamente 55887 nós.

Modelos de material para calibração térmica e as simulações de tensão
Modelo de Três Barras
O modelo de três barras considerado é baseado em dois apoios transversais com dimensões de 100x40x20 mm responsáveis por limitar a liberdade de movimento entre as barras e três barras cilíndricas verticais idênticas com raio de 5 mm e comprimento de 100 mm. Para evitar possíveis erros de simulação devido à concentração de tensões (efeito geométrico), foram adicionados flanges de 5 mm de raio na parte superior e inferior das barras. Para simular os aspectos térmicos, a faixa central foi dividida em três partes, o volume cilíndrico e as duas regiões do flange.
No limite entre essas regiões, foi definida uma condição de isolamento térmico para que a superfície adicional das mesas não crie um gradiente térmico na região cilíndrica, além de impedir o fluxo de calor para os apoios transversais. Para todo o volume da faixa central, o aquecimento foi aplicado desde a temperatura ambiente (22 °C) até uma temperatura de aproximadamente 1325 °C, seguindo um perfil de aquecimento observado durante a calibração da fonte de calor, mostrado pela linha vermelha na figura. 4.12. A partir do tempo 21 s, foi aplicada uma condição de resfriamento com um coeficiente de convecção de 455 W/m2°C e um coeficiente de emissividade de 0,8.
Esses valores foram usados para garantir um t8/5 de 12 s, resultando em uma taxa de resfriamento de 25 °C/s. Para a análise de tensões, um suporte fixo foi aplicado na superfície superior do suporte transversal superior e na parte inferior do suporte transversal inferior.

Modelo Termomecânico de Chapa
Esta condição foi aplicada para limitar o movimento do modelo no espaço (movimento do corpo rígido). As áreas amarela e vermelha foram combinadas e atribuídas ao modelo de material P1300, enquanto as áreas turquesa e azul foram aplicadas aos modelos P1150 e P920, respectivamente. Para fins de comparação, também foram realizadas simulações considerando a placa inteira com os materiais P1300, P1150, P920 e PCTE.
Assim, foi possível avaliar os efeitos de considerar ou não a transformação martensítica (expansão térmica) no campo de tensões residuais, além da influência de Tp em Ms e consequentemente na resposta do modelo termomecânico. Com os mesmos objetivos do modelo de três barras, para consideração das simulações mecânicas, foi aplicada uma condição de imobilidade ao plano lateral direito do modelo. A escolha de aplicar esta condição entre os lados direito e esquerdo foi feita de forma arbitrária e deve-se notar que isso não implicou em nenhuma mudança na simetria dos planos.
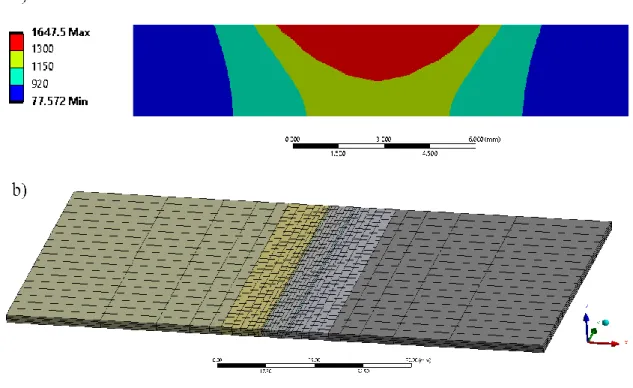
Calibração do Modelo Térmico
Segundo Araújo et al. 2017), uma temperatura de 1336 °C foi usada como limite para a região de fusão, que é representada pela linha vermelha na Figura 5.2. Os parâmetros considerados da fonte de calor foram uma eficiência de arco de 0,8 e uma distância radial de 3,1 mm. Juntamente com a correlação dos dados do termopar, eles reforçam a hipótese de que as aproximações utilizadas durante a construção do modelo térmico foram adequadas e que a fonte de calor utilizada é adequada.
A Figura 5.4 mostra regimes simulados de aquecimento e resfriamento de placas em diferentes intervalos de tempo, em forma de contorno de cores. Olhando para os resultados da calibração da fonte de calor, conclui-se que os métodos utilizados foram eficazes. A utilização do modelo de material descrito por Deng e Murakawa (2006) como base para a descrição do comportamento da chapa utilizada para o procedimento de soldagem e aquisição dos perfis térmicos;
A aplicação de um modelo de simulação desacoplado e as consequentes simplificações que esta consideração implica, como mostra a Figura 3.5;. A aplicação da fonte de calor gaussiana para simular uma soldagem GTAW de chapas finas, como nos trabalhos de Araújo et al.

Modelo de Três Barras
Os resultados das tensões residuais perpendiculares ao eixo Y bem como uma representação das deformações para os diferentes Tp podem ser vistos na figura 5.8 à figura 5.11. Outro dado relevante foi que o aumento das temperaturas de Ms e Mf para cada um dos modelos de material levou a um aumento da deformação observada nos estados finais, porém o modelo PCTE apresentou uma deformação intermediária, os valores de deformação podem ser observados na Tabela 5.5. Para a análise dos estados finais de tensões observados nas simulações dos três modelos de barras, foram levados em consideração os valores absolutos dos oito elementos mais centrais da viga central (Figura 5.12).
Essa consideração foi feita principalmente porque a localização dos pontos de tensão máxima e mínima ao longo da barra central não coincidiam, dificultando uma avaliação consistente. O desenvolvimento dos estados de tensão durante o resfriamento para os diferentes modelos de materiais pode ser visto na Figura 5.13. Analisando os resultados de cada modelo de material, no Modelo PCTE, as tensões atingem um valor máximo de 1236,3 MPa, apresentando uma curva continuamente crescente durante o resfriamento.
Por outro lado, para os modelos onde se considera a transformação martensítica, observam-se “vales” a partir da marca dos 45 segundos, que coincidem com as temperaturas Ms e Mf para cada um dos modelos de material. Os resultados dos Modelos de Três Barras reforçam os achados de estudos como Lee e Chang (2011), Deng (2009) e Deng e Murakawa (2006) que replicam a.

Modelo Termomecânico de Chapa
Para analisar os perfis de tensão de cada um dos modelos simulados, três linhas cruzando toda a largura do modelo e com profundidade de 1,5 mm e a 25 mm, 50 mm e 75 mm do ponto de origem foram selecionadas como referências. do modelo de solda como mostrado na Figura 5.15. Os maiores picos foram observados para a linha de referência de 75 mm, com aproximadamente 90 MPa em tração e 70 MPa em compressão a 2,44 mm à esquerda e à direita do centro da solda, conforme Figura 5.16. As Figuras 5.17 a 5.21 mostram os estados finais das tensões residuais na direção X (perpendicular à solda) na profundidade de 1,5 mm para todos os casos estudados.
A Figura 5.22 ilustra uma comparação mais detalhada dos perfis de tensão analisados na linha de referência de 50 mm. Ao contrário da Figura 5.22, os gráficos representados na Figura 5.23 e na Figura 5.24 mostram os perfis de tensões perpendiculares a X nas linhas de referência de 25 e 75 mm, respectivamente, regiões que, devido às bordas do corpo, deixaram de constituir um quase- regime estacionário em relação à temperatura. O próximo conjunto de figuras, Figura 5.25 a Figura 5.29, mostra os estados de tensão residual final na direção Y (paralela ao cordão de solda) a 1,5 mm de profundidade.
Na área mencionada, é possível observar uma diminuição da tensão residual com a diminuição do Tp considerado no modelo de material. Avaliando o gráfico da linha de referência a 50 mm do início do cordão de solda, na Figura 5.30, o modelo P1300, que possui as maiores temperaturas Ms, apresentou diferenças de aproximadamente 50 MPa e 100 MPa, respectivamente, no centro da solda e em HAZ em relação ao caso com material P920. Assim como na Figura 5.23 e na Figura 5.24, os gráficos mostrados na Figura 5.31 e na Figura 5.32 mostram os perfis de tensão em regiões fora do regime quase estacionário em termos de fluxo de calor.
A maior diferença observada está no gráfico para a linha de referência de 75 mm (Figura 5.31), em que o comportamento dos materiais que levou em conta a transformação martensítica foi muito semelhante e apresentou um pico secundário de aproximadamente 200 MPa.
