Mat. Res. vol.8 número4
Texto
Imagem

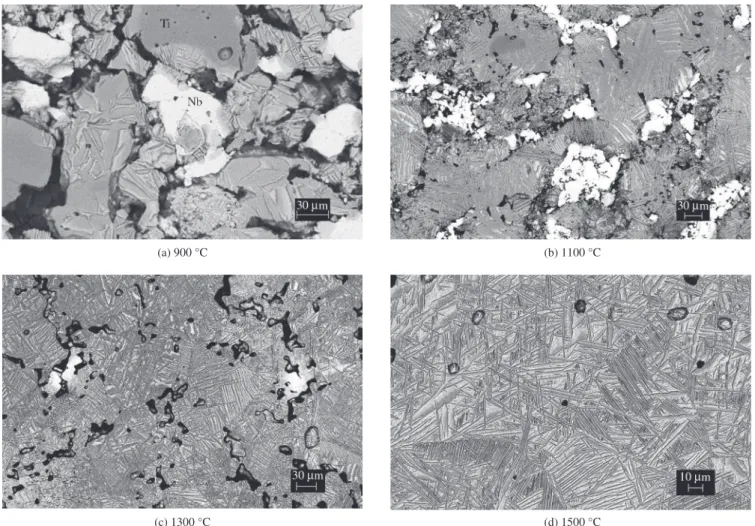

Documentos relacionados
Based on these ideas, a broad programme of tests is under devel- opment involving other levels of stress and temperatures in the range from 500-700 °C, with rupture times going up
For higher stress values (Figure 9), the fractured surface has mainly overloading areas; with apparently little crack propagation regions.. With the reduction of the stresses
In the Q&P process, high carbon supersaturation of the martensite prior to partitioning could conceivably drive transition carbide formation to a greater extent
the microstructure of varistors exhibit considerable variation from one manufacturer to another, they all exhibit the characteristics of a typical ceramic prepared by
Values predicted by the mean square displacement are slightly higher than those obtained from the jump frequency, and non basal jumps have higher vacancy migration frequency than
It is important to emphasize that the Ti-13Nb-13Zr alloy presents lower initial elastic modulus and higher ultimate tensile strength, when compared with the other studied
The Ti-35Nb samples presented high densiication, around 70% of the theoretical density, after cold isostatic pressing and, among 93 and 95%, after sintering above 1600 °C,
One important feature of the Brazilian Tecnored ironmaking process is its lexibility to use different types of solid fuels, other than metallurgical coke, as proved in the pilot